Tips & Tricks
The Versatility of OMAX Abrasive Waterjets
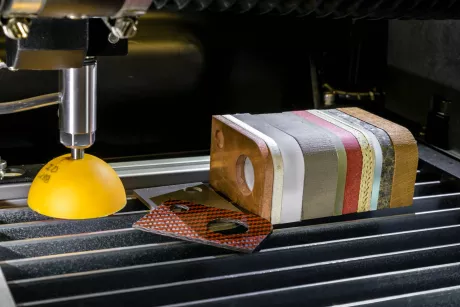
A state-of-the-art machine tool cutting aluminum, and glass, and steel, and rubber, and composite, and …
Innovation changes how and what we machine. On top of that, industry trends fluctuate with market prices of imported or locally sourced materials. If the price of steel wavers, how will your company react? When the needs of the customers change, how will your machine shop adapt? Can you justify the cost of updating single purpose machinery? With the versatility of an OMAX abrasive waterjet, you and your company are ready for whatever material changes may happen in the future.
In terms of types of material cut, an abrasive waterjet is the most versatile cutting method available. Where EDM specifically cuts conductive substances, and laser is limited to non-reflective materials, abrasive waterjet cuts virtually every material available. OMAX machines are currently being used to cut stone, brass, carbon steel, glass-refined plastics, and so much more. With abrasive waterjets, there is no need for special coatings or other considerations. Materials simply need to be fixtured into place. With abrasive waterjet, the cut product has no heat affected zones (HAZ) or material distortion, often removing the need for secondary machining.
In addition, abrasive waterjet is pushing the extremes of micro and macro machining. OMAX’s MicroMAX JetMachining Center is capable of a positioning accuracy within five microns and is being used for extremely small precision customization in the defense and tech industries. Using the same technology, the OMAX 120X series, offered with a customizable cutting bed that can reach up to 40 feet by 10 feet, is being used in large tank fabrication as well as architectural metal and glass. The size of the finished product is only limited by the size of the waterjet’s cutting table, allowing a manufacturer to work as small or as large as needed without additional specialty equipment.
Switching between materials is as fast a placing a new material on the cutting bed. An abrasive waterjet is capable of cutting aluminum one minute then switching out to cut foam rubber the next. What if a fabrication shop client asks for a prototyped part in titanium, then also asks for a gasket to accompany it? Depending on the programming time of the part needed, it isn’t out of the question to have the entire project wrapped up in one day, employing one person, on one abrasive waterjet.
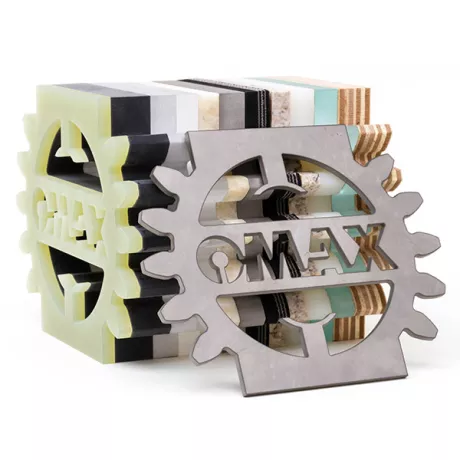
The versatility of an OMAX abrasive waterjet stems from the integration of OMAX’s IntelliMAX software. With Intelli-MAX, the operator enters the material type and thickness, then the software calculates and controls the cutting. The machinability is already factored in. If an operator entered in a new design into the Intelli-MAX MAKE program (the program that controls the waterjet), they will be prompted by a screen with a dropdown for the type of material. This dropdown list contains over sixty different materials ranging from red oak to Inconel to PVC and everything in between. Additional materials can be entered in manually. After an operator enters the material and thickness, they are ready to cut. At any time, an operator can reset the material by a simply click of a button.
You may be cutting mild steel today, but what about tomorrow? For fabrication shops, single purpose machines can be a deal breaker; and for manufacturers, it can be limiting. Shops don’t want to turn away customers due to inadequate capabilities. Manufacturers don’t want to eat the cost of retooling with product changes. In the rapidly changing world of machining, you need a tool that can accommodate variation. With an OMAX abrasive waterjet, you can be assured you have the right cutting tool to easily work whatever material your company may come across.