The OMAX 120X is ideal for multiple-part projects or large-scale part production.
- Available in a range of lengths from 33' 3" to 51' 6" feet (10.13 m to 15.70 m)
- ±0.001" (±0.025 mm) linear position accuracy
- Backed by our exclusive IntelliMAX Premium Software
- Advanced high-precision IntelliTRAX linear drive technology designed exclusively for the abrasive waterjet environment
- Standard programmable Motorized Z-Axis with a precision OMAX MAXJET 5i Nozzle boosts productivity and process efficiency
- Standard Rapid Water Level Control for cleaner, safer, and quieter submerged cutting completes most work below 80 dBA
- Standard 600 lb Bulk Abrasive Delivery System transports garnet from the assembly's large hopper into the Zero Downtime Hopper located on the Z-Axis
- Standard scissor-style hard plumbing
- Designed and manufactured at the OMAX factory in Kent, Washington, USA
- Does not create heat-affected zones or mechanical stresses
- Machines a wide range of materials and thicknesses, from metals and composites to glass and plastics
- No tool changes & minimal fixturing dramatically reduce setup
DIMENSIONS & SPECS
120X-S | 120X | 120X-1 | 120X-2 | 120X-3 | |
Footprint (with pump) | 26' 7" x 19' 5" (8.10 m x 5.92 m) | 33' 3" x 19' 5" (10.13 m x 5.92 m) | 37' 2" x 22' 5" (11.33 m x 6.83 m) | 44' 1" x 22' 5" (13.44 m x 6.83 m) | 51' 6" x 22' 5" (15.70 m x 6.83 m) |
Height (with scissor plumbing) | 14' (4.27 m) | 14' (4.27 m) | 14' (4.27 m) | 14' (4.27 m) | 14' (4.27 m) |
Operating Weight | 58,961 lbs (26,744 kg) | 71,679 lbs (55,997 kg) | 88,937 lbs (44,096 kg) | 106,195 lbs (48,169 kg) | 123,453 lbs (55,997 kg) |
Weight (tank empty) | 22,000 lbs (9,979 kg) | 22,000 lbs (9,979 kg) | 26,000 lbs (11,793 kg) | 30,000 lbs (13,608 kg) | 34,000 lbs (15,422 kg) |
X-Y Cutting Travel* | 13' 4" x 10' (4.06 m x 3.04 m) | 20' x 10' (6.09 m x 3.04 m) | 26' 8" x 10' (8.12 m x 3.04 m) | 33' 4" x 10' (10.16 m x 3.04 m) | 40' x 10' (12.19 m x 3.04 m) |
Z-Axis Travel (with Motorized Z Axis)* | 8" (203 mm) | 8" (203 mm) | 8" (203 mm) | 8" (203 mm) | 8" (203 mm) |
Table Size | 14' 11" x 11' 5" (4.55 m x 3.48 m) | 21' x 11'5" (6.40 m x 3.48 m) | 28' 3" x 11' 5" (6.40 m x 3.48 m) | 34' 11" x 11' 5" (10.64 m x 3.48 m) | 41' x 11' 5" (12.50 m x 3.48 m) |
Material Supports Slats | 4" x 1/8" Galvanized Steel |
---|---|
Maximum Supported Material Load | 400 lbs/sq ft (1,950 kg/sq meter) |
Electrical Requirements | 3-Phase, 380-480 VAC ±10%, 50-60 Hz |
Noise Level | Below 80 dBA at one meter for submerged cutting |
Speed | 350 in/min (8,890 mm/min) |
Linear Positional Accuracy* | ±0.001" (±0.025 mm) |
Repeatability* | ±0.001" (±0.025 mm) |
Ballbar Circularity* | ±0.005" (±0.127 mm) |
* Accessories may reduce travel. Accuracy specifications are at 72° F (22° C) .
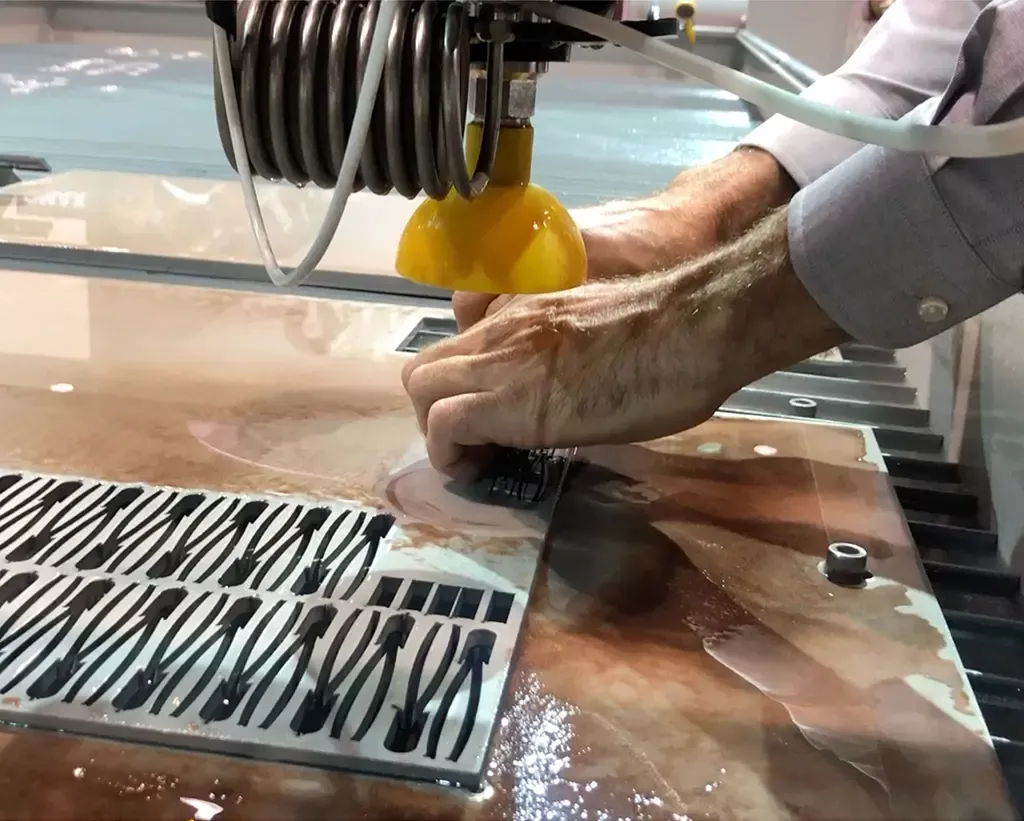
PUMP INFO
Maximized uptime with 1,000 hours between maintenance cycles
Increased production by delivering 30% more cutting power
Variable Frequency Drive reduces startup power consumption and maximizes operating flexibility
EnduroMAX 100 HP | EnduroMAX 50 HP | EnduroMAX 30 HP | DynaMAX 575P | |
---|---|---|---|---|
Motor Power | 100 HP (75 kW) | 50 HP (37kW) | 30 HP (22 kW) | 75 HP (56 kW) |
MAX Jet Power | 85 HP (63 kW) | 42.5 HP (31.5 kW) | 25.5 HP (18.7 kW) | 51.6 HP (37.9 kW) |
Output Pressure | 60,000 psi | 60,000 psi | 60,000 psi | 60,000 psi |
Orifice & Flow Rate ** | 0.022" / 2.25 gpm (0.56 mm / 8.52 lpm) | 0.016" / 1.20 gpm (0.41 mm / 4.54 lpm) | 0.012" / 0.67 gpm (0.30 mm / 2.54 lpm) | 0.017" / 1.5 gpm (0.43 mm / 5.68 lpm) |
Footprint LxWxH | 44" x 62" x 44" (1,118 mm x 1,575 mm x 1,118 mm) | 66" x 36" x 38.5" (1,676mm x 914mm x 978mm) | 66" x 36" x 38.5" (1,676mm x 914mm x 978mm) | 40" x 79" x 59" (1016 mm x 1996 mm x 1509 mm) |
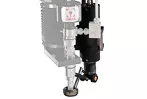
Collision Sensing Terrain Follower
The Collision Sensing Terrain Follower is an essential tool for working with uneven surfaces.
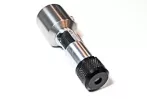
Laser Feature Finder
The Laser Feature Finder allows for visual reference before introducing water and garnet.
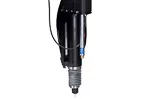
OMAX Drill Head
Achieve reliable piercing of composites and laminates with an OMAX-Engineered pneumatic drill.
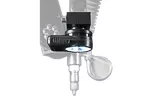
Precision Optical Locator
The Precision Optical Locator is designed to let you accurately place parts on the OMAX for secondary machining operations.
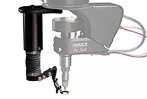
Terrain Follower
Used with the AJet cutting head, the Terrain Followers adjusts standoff to compensate for irregularities in the material surface.
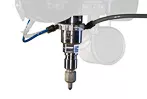
Vacuum Assist
The OMAX Vacuum Assist is ideal for piercing brittle materials, advanced composites, challenging laminates, and more.
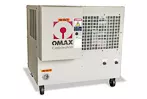
Chiller System
OMAX Chiller supplies inlet water at a consistent temperature extending pump seal life for longer, sustainable production.
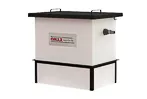
Laminar Filter
The Laminar Filter cleans overflow required for recycling through a closed loop system or for sanitary disposal.
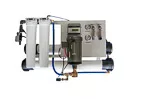
Reverse Osmosis System
The Reverse Osmosis System can remove 90% of total dissolved solid in water.

Water Recycling System
The OMAX Water Recycling System captures and reuses workable overflow water.
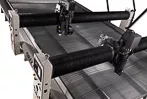
DualBRIDGE System
The DualBRIDGE System is a configuration option that allows the addition of a second Y-bridge to boost efficiency and flexibility.
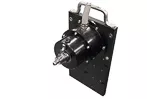
Rotary Axis
The Rotary Axis allows for 6-axis paths to create complex 3D shapes in tube, pipe, and bar stock.
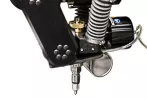
TiltaJET
The TiltaJET lets the OMAX JetMachining Center achieve virtually zero taper.
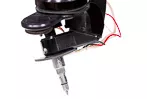
AJet
With a cutting range from 0° to 60°, the AJet can easily cut beveled edges, angled sides, and countersinks.