
LEARN ABOUT WATERJETS
LEARN ABOUT WATERJETS
THINGS TO CONSIDER BEFORE BUYING A WATERJET
Like when making any major machine tool purchase, there are factors to think about. What and how you are cutting, the floor space of your shop, and the needs of your clientele are just the beginning of the discussion. Below is a series of questions and rationales around the using and purchasing of a waterjet.
WHAT MATERIALS WILL I BE CUTTING?
Waterjets can cut almost any material. Pure waterjets can quickly and accurately cut soft materials such as rubber, foam and other gasket material.
Abrasive waterjets can cut almost any other material over a very wide range of thicknesses:
- Virtually all metals, including hardened tool steel, stainless steel,
aluminum, copper and titanium - Non-tempered glass, including multi-layer laminated safety glass
- Composites
- Laminates
- Stone
- Most ceramics
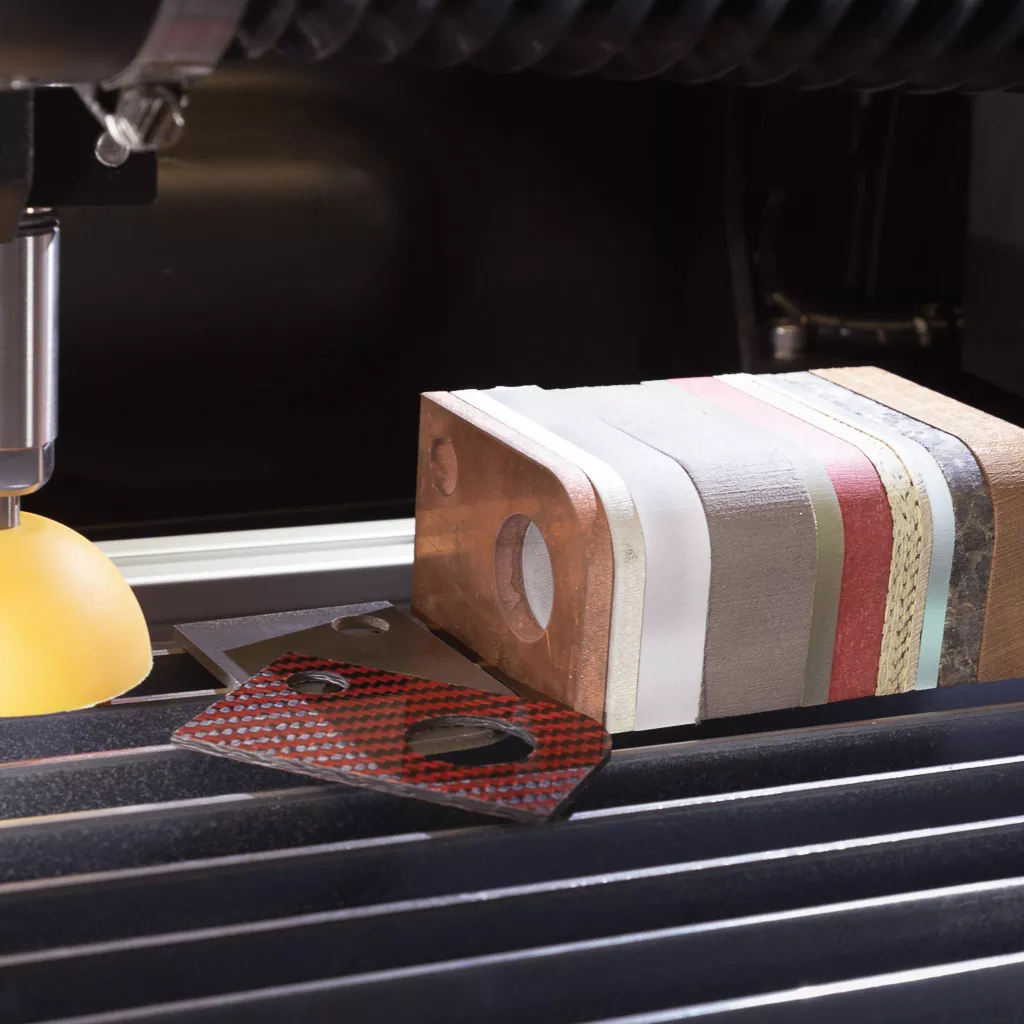
HOW MANY PARTS WILL I BE CUTTING?
Set-up time for a waterjet with an advanced control system is minimal. Advanced control software (such as the OMAX IntelliMAX Software Suite) can automatically program the cutting path of a desired part directly from a CAD drawing. Just lightly secure the material stock to the cutting table and enter the material type and thickness into the control computer. The control system does the rest and an accurate part is produced on the first run. This capability makes waterjet a perfect process for short-run and one-off production parts. At the same time, modern nesting software means that waterjets are also ideal for mass production of parts with minimum waste.

WHAT SIZE TABLE WILL I NEED?
Waterjet cutting table are now available in a wide range of standard sizes, ranging from small 2' 5" x 2' 2" (737mm x 660mm) tables to very large 26' 8" - 46' 8" x 13' 4" (8.1m - 14.2m x 4m) tables. The two considerations in selecting a table size are the size of part to be made and the size of stock material to be used. It is generally easiest and most economical to err on the side of a larger table that will handle all intended material stock sizes and future larger parts. However, sometimes space limitations mandate a smaller size. As a result of the design of our tables, OMAX offers the smallest footprint relative to the table size thereby conserving valuable shop floor space.
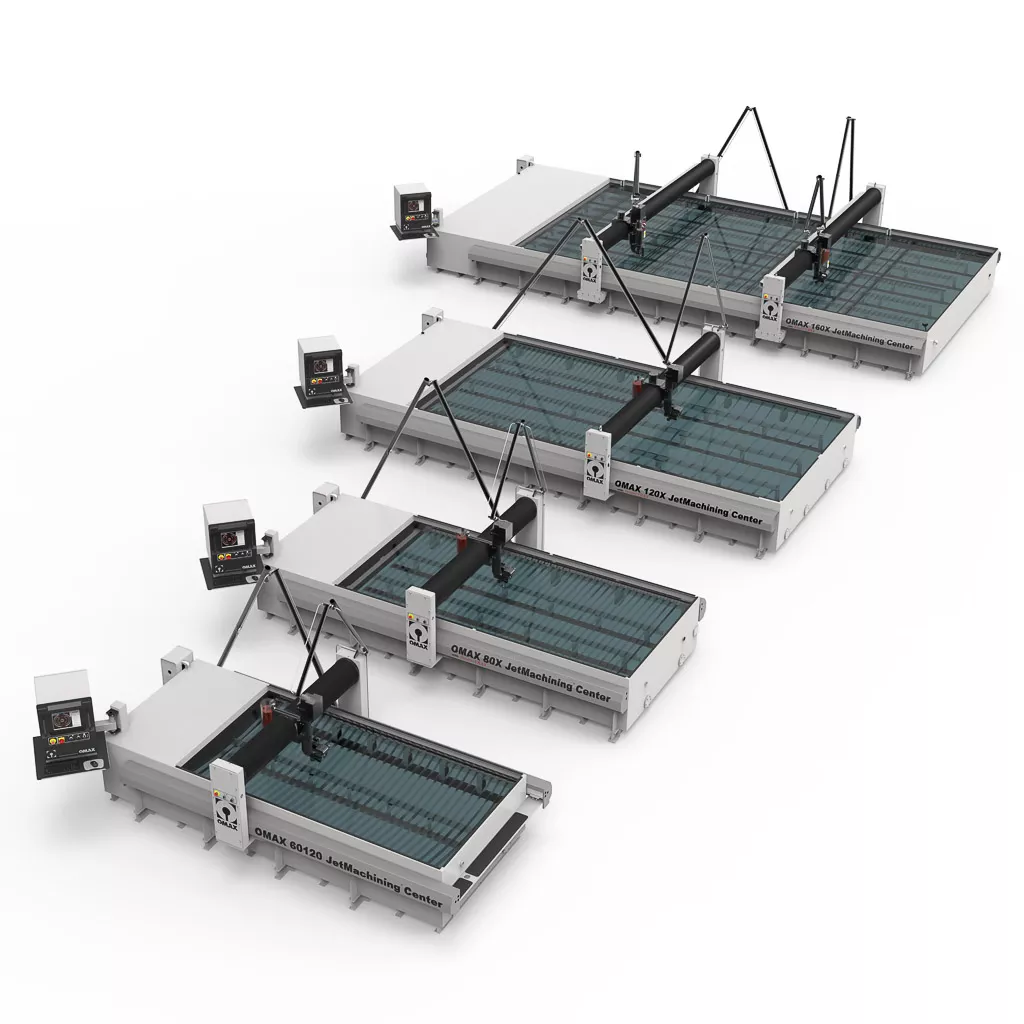
WHAT KIND OF SPECIAL FEATURES WILL I NEED?
Water cutting has some special characteristics that make it particularly attractive for some applications:
WATERJETS CUT WITHOUT HEAT.
This means that there is no thermal distortion to complex and intricate parts and no heat affected zone that might change material properties. It also means that secondary machining processes, such as thread-tapping, are easily carried out on a waterjet-cut blank. Waterjets make a very narrow cut and have very low cutting forces. This frees part designers to create intricate parts that would be virtually impossible to make with conventional manufacturing processes. Very complex shapes and contours are easily possible with waterjet cutting. An additional benefit when expensive material is being machined is low waste costs.
ADVANCED MOTION CONTROL.
This permits production of precise parts. Traditional waterjets cut parts to a precision in the range of ±0.010" (0.25mm). However, by using mathematical models to account for and correct the natural error-creating curvature of a moving waterjet, modern high-precision waterjets with advanced control systems such as the OMAX IntelliMAX Software Suite can make parts to a general tolerance of ±0.005" (±125μ). The most advanced systems have computer-controlled taper-compensation cutting heads and can control key part dimensions to an accuracy of ±0.001" (±25μ).
Waterjet Advantages

WHAT KIND OF WATER AND WASTE FACTORS SHOULD I CONSIDER?
Early waterjets had a well-earned reputation for being noisy and dirty. An exposed water jet is noisy and an exposed abrasive waterjet can throw a lot of abrasive dust into the air. However, these factors are eliminated in modern systems by simply cutting under a thin layer of water. The water layer reduces the noise level to below that of most machine tools and eliminates the dust by keeping the particulates in the water. An abrasive waterjet machine cutting under water can be placed anywhere that you might place a conventional machine tool. No noxious fumes or smoke is generated, and the part does not become contaminated with cutting oils.
A waterjet machine generates two waste streams. Excess water containing very small amounts of solid fines, which can be filtered if required by local regulation and then sent directly to a waste water drain. Kerf material and garnet waste can be sent to a landfill. If the material being cut is poisonous—lead or beryllium, for example—both waste streams must be cleaned to meet environmental regulations and the water may be recycled.
WHAT ARE THE COSTS TO RUN AND MAINTAIN A WATERJET?
An abrasive waterjet machine costs between $25 - $30 per hour to operate for consumables and maintenance parts. At operating pressures above 60,000 PSI (4,137 bar) more maintenance is required and unplanned downtime can increase dramatically. Ultra high pressures result in higher operating costs due to accelerated metal fatigue in high pressure components used in pumps and plumbing. For this reason, waterjet cutting machines usually operate most economically and reliably in the range of 60,000 PSI (4,137 bar) or less.
Maintenance items include all parts wetted by the high-pressure water and all parts through which abrasive flows. Nozzles parts such as mixing tubes can last 30 to 60 hours, while jewel orifices last over 500 hours and pump seals are replaced near 1,000 hour intervals.
New troubleshooting and maintenance techniques must be learned for successful operation of waterjet equipment, but the skills to be learned are not difficult, and thousands of machines are successfully and profitably run and maintained by their owners and operators.
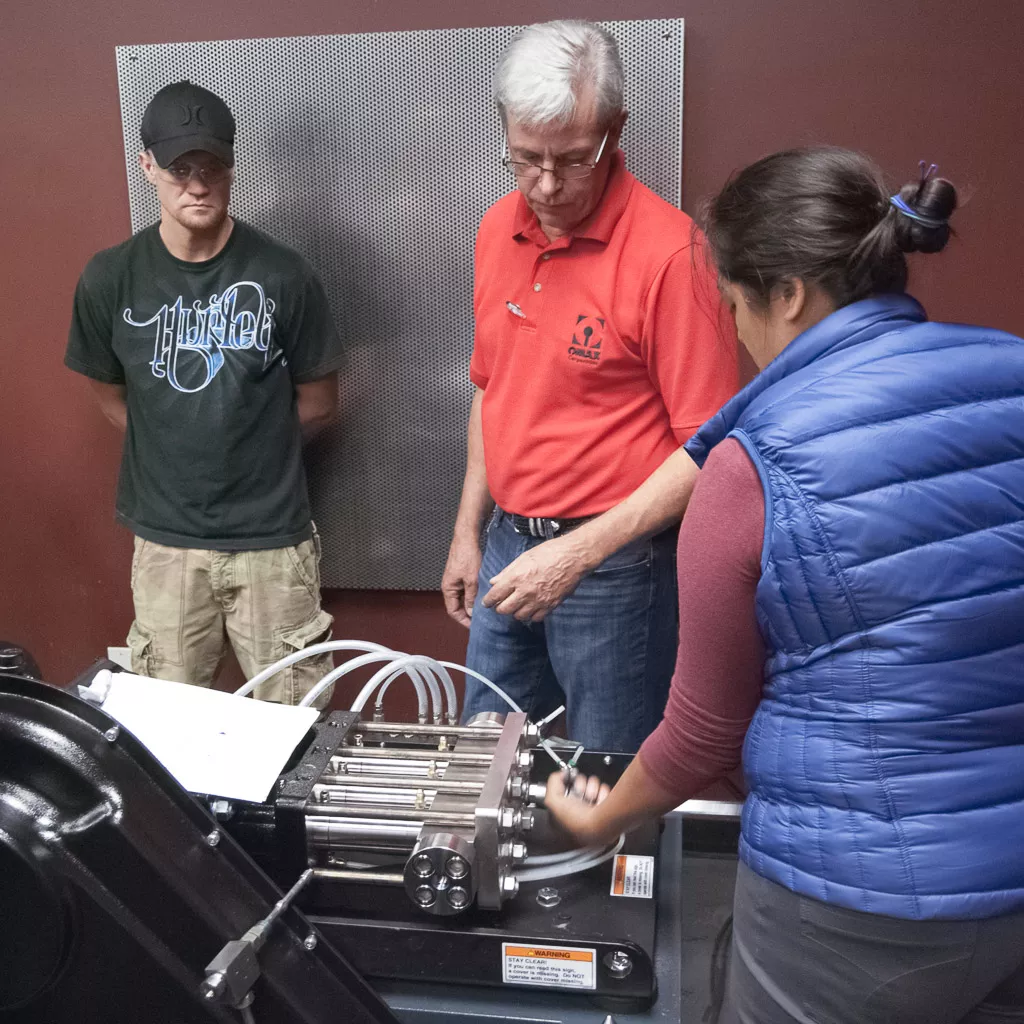
RELATED QUESTIONS
A number of factors go into calculating waterjet operational costs, including but not limited to consumable parts, pump horsepower, water supply cost, whether the machine is running one cutting head or two, abrasive cost, the type and thickness of the material being cut and the desired edge quality. Because of all these variables, the specific answer is, it depends on what you're doing with the waterjet. However, a very general operating cost range to run an OMAX waterjet is UDS $25-35 per hour, not including labor cost.
At operating pressures above 60,000 PSI (4,137 bar) more maintenance is required and unplanned downtime can increase dramatically. Ultra-high pressures result in higher operating costs due to accelerated metal fatigue in high pressure components used in pumps and plumbing. For this reason, waterjet cutting machines usually operate most economically and reliably in the range of 60,000 PSI (4,137 bar) or less.
Prudent machine shops calculate their service prices based on the price per part. OMAX software is the most accurate in the industry at predicting the cutting time and cost for a specific part. The cost data can be used for internal accounting reports or customized to include labor and other overhead costs to create a customer quote, all within the Intelli-MAX software.
What to do with that used abrasive tends to fall into three categories: disposing, recycling, and re-purposing. In most cases, used abrasive from a waterjet can be thrown out with other non-toxic garbage since garnet is a non-reactive, natural substance. However, if the abrasive has been used to erode toxic material and is contaminated with particles of toxic material such as lead or beryllium, it can't be simply thrown out with the trash and must be treated as toxic waste. A service that will periodically collect and properly dispose of your used abrasive can be employed to simplify this process.
For most locations in the U.S. and Canada, the answer is “no”. Most of the water that comes from a city's water supply in these countries can be used in an abrasive waterjet without any treatment. For those areas that fall into the exception, waterjet owners can save significant time and money by conditioning the water, no matter what brand of waterjet machine they're running. OMAX recommends all waterjet purchasers get a water quality analysis before buying. The water should be tested for "total dissolved solids" (TDS), not just for bacteria. Dissolved minerals in the water can do a lot of damage to the high-pressure equipment. Even if the parts per million of dissolved solids in your water initially tested within the allowable limit (typically at or below 250 ppm), you should periodically retest. Water quality can change when there is unusual weather or your water department switches reservoirs.
Read more at Do I Need To Treat The Water For My Waterjet? »