Tips & Tricks
Why Abrasive Waterjet Software Matters
Other cutting technologies use solid-material tools with fixed shapes, but abrasive waterjets use liquid sandpaper to cut solids, and that liquid constantly changes shape in response to part geometry, material thickness and density. The right software is critical to optimize the cut.
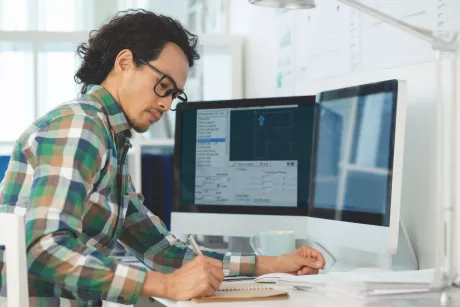
OMAX built its IntelliMAX software suite to model the performance of its hardware so it could control every aspect of a cut. Rather than just maximizing the feeds and speeds that dominate the approach to part programming on other waterjets, OMAX software focuses on cut quality and assigned the correct feeds and speeds to achieve it, creating thousands of instructions per inch of cutting path in a patented process. To this day, those capabilities remain unique among abrasive waterjet control software.
The first two generations of cutting algorithms in OMAX software were better equipped to choose the right speeds for straight-line cutting. As a result, the program slowed the cut to accommodate the output. Because the exit point of the cutting jet tends to lag behind the entry point on an abrasive waterjet, the top of the jet reaches a corner before the bottom of the jet if the cut moves at a constant speed. To overcome that and produce a perpendicular jet stream, the software slowed the cut, and in early software versions, that slowdown represented a conservative approach to geometries and cut behavior.
As OMAX software evolved, we learned how and when to slow or speed up the cut to accommodate optimal geometry and cut-quality results. Instead of following a right-angled path to cut corners, we discovered a more-efficient approach would cut past the corner, jump back and change directions by 90°. This resulted in the development of the corner passing technique, now an automatic function within OMAX waterjet software.
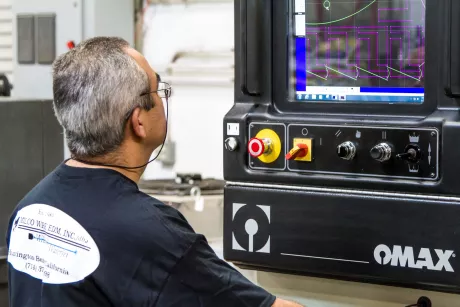
Our investment in software has proven to be a game changer in productivity. Whereas the first generation of OMAX software could cut 26 inches of an 8-toothed gear-shaped tool path from 1" stainless steel in 30 minutes, the third software generation achieved another 3 inches of a 9-toothed gear in the same amount of time. By its fourth generation, the software could cut 64 inches of a 20-toothed gear in that half hour, using the same pump and garnet flow rate as the previous software generations.
The efficiency and power of our pumps makes it possible for us to cut straight lines at high speed, but it is our software that makes the difference to cut more-complex geometries, speeding up wherever possible and slowing only when it must. OMAX never stops enhancing software functionality and productivity. Our fourth-generation application carries 17 patents for a host of innovations. Our understanding of cutting geometry leads our industry. We've poured the results of thousands of cutting trials on hundreds of materials into the IntelliMAX software suite, and those years of data enable us to deliver precision you can rely on for optimal tool paths, speed and material capabilities.
All these improvements came solely through enhancing our software.