Customer Success: Educational Institutions
Missouri S&T: Applying Design Solutions for Today
Machine: MAXIEM 1515
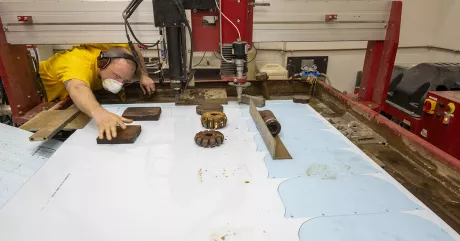
For over 20 years Missouri University of Science & Technology (S&T) has been using OMAX products to design, test and create a variety of projects geared towards molding the next generation of engineers. Missouri S&T integrates education, research and application to create and convey knowledge that serves our state and helps solve the world’s great challenges. It is with that mission that the school has utilized their Student Design Center (SDELC) to produce PPE in the wake of the current Covid-19 pandemic.
Community Stewardship
“Phelps Health, a local healthcare provider, contacted the University on March 21, just after the decision to shut down the University and as Spring Break was starting,” explained Dr. Chris Ramsay, Director of SDELC at Missouri S&T. They needed face shields – and Missouri S&T’s design and manufacturing capabilities were more than up to the task
In just two days, prototypes had been designed, tested and approved by Phelps Health. After getting the green light to go ahead with manufacturing, Ramsay said, “The decision to use the waterjet was made in these first few days, when the volume of face shields that would be needed was determined. In less than 10 days, the face shields were being used by Phelps Health nurses and doctors on the Phelps County COVID-19 testing site set up at Phelps Health.”
Currently, the school uses a MAXIEM 1515 JetMachining Center with a bulk hopper and A-Jet. Designed to deliver high performance in a compact package, the MAXIEM 1515 is an excellent fit for a wide range of applications thanks to an ample cutting area that easily fits most material stock. The A-Jet is a completely software-controlled multi-axis cutting head that greatly expands the versatility of the OMAX JetMachining Center, including the MAXIEM line. Advanced features in the IntelliMAX Software Suite allow the A-Jet to compensate for taper and easily create complex 3D shapes.
Due to the ongoing pandemic, manufacturers, fabricators and schools are focused on leveraging their equipment to find creative solutions. With the advancement in machine tool usability, functionality, and versatility, many fabrication spaces are better equipped than ever for both rapid prototyping and high production manufacturing. Because of this, students and staff at Missouri S&T were able to use their MAXIEM 1515 to make a big impact.
For the COVID-19 design project, “The waterjet was used to cut individual face shields from poly sheets, creating more than 6,000 face shields, as well as another 3,000 face masks for use by Phelps Health,” said Ramsay. “The complete project provided 9,000 pieces of personal protective equipment for Phelps Health medical staff and other area healthcare providers, as well as local first responders, fire and law enforcement departments.”

Waterjet Machining Versatility
Naturally, Missouri S&T uses their design center and waterjet for much more than this PPE project. Nineteen student-led design teams take on engineering challenges ranging from race cars to robots. These teams provide over 1,300 S&T students with leadership, networking and technical learning opportunities through industry-sponsored design competitions. Other students get life-changing global experience by tackling economic and healthcare-related infrastructure problems in developing nations.
“We have nineteen design teams making nineteen different projects every year, and all of them have a manufacturing component,” explained Ramsay, “whether the Mars Rover, Aviation, Autonomous drones both underwater and flight, two Formula 1 race cars, one powered by combustion and the other by electric motors.”
The design center uses the MAXIEM 1515 waterjet to fabricate everything. This has included a huge range of projects, such as the frames, suspensions and mounting assemblies for chemical reaction chambers and motors, or carbon fiber and aluminum sheets for aerospace components and performance racing car bodies. “We use it for everything from plastics and poly to steel, aluminum, composites, foam, rubber, brass, and titanium. From super thin materials to five-inch plates,” said Ramsay. Because of this versatility, the school is able to take on much more. “The waterjet opens the door to new possibilities of design and manufacture at the highest levels of accuracy, and it has allowed a generation of students to gain an ability to create far beyond expectations.”