Media Center
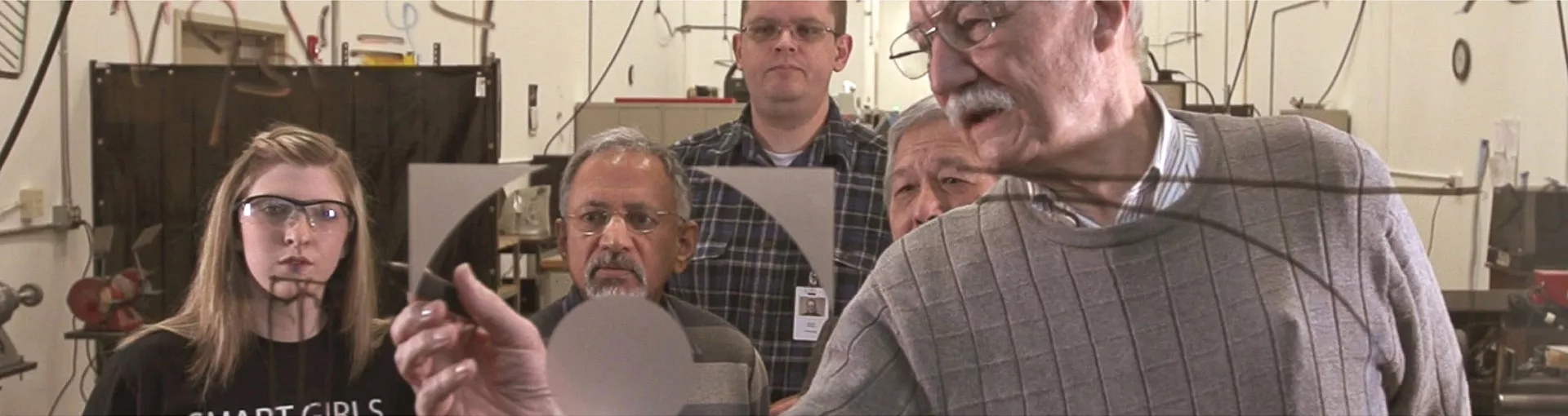
MEDIA CENTER
Tips and Tricks
Four Reasons To Always Use OMAX Genuine Parts
We’ve all done it: snapped up a generic, aftermarket replacement part or consumable in the quest to save a few dollars. But while the desire to cut costs is understandable, how much are we giving up in return for those short-term savings, and is it really worth it in the long run? Read
The Smart Choice: Buying American-Made Machine Tools
Choosing the right manufacturer is critical for ensuring high performance, durability, and long-term value when purchasing machine tools. In an increasingly globalized economy, many companies are tempted to outsource production to cut costs. That may not be the right option. Read
Abrasive Waterjet Machines: The Cutting Edge for Defense Manufacturing
Learn how abrasive waterjet cutting technology from OMAX provides efficient, flexible and profitable part processing for the defense industry. Read
Press Releases
Jake Brown Named Hypertherm Associates EVP, Global Sales and Marketing
Hypertherm Associates, a U.S. based manufacturer of industrial cutting systems and software, announced that Jake Brown, previously Vice President for the Americas Region, has been named Executive Vice President of Global Sales and Marketing, overseeing all sales, marketing, and service strategy and execution for the global enterprise Read
Hypertherm Associates and BLM GROUP form a strategic partnership
Hypertherm Associates and BLM GROUP announce a strategic partnership agreement aimed at expanding the market reach of their respective solutions. The two industry leaders will collaborate to offer premier solutions to customers through BLM GROUP’s laser cutting and tube bending systems and Hypertherm Associates’ plasma and waterjet cutting products and software. Read
Hypertherm Assoc. innovates at EuroBLECH 2024 with an immersive booth
At EuroBLECH 2024, Hypertherm Associates will bring together its cutting-edge technologies under one roof in Hall 13, Booth E158, where visitors can explore the full spectrum of industrial cutting solutions. Read
News Articles
Jetting to success
A New York-based shop implements waterjet technology and gains value Read
Digging deep
Fabricating projects in the engineering program’s shop helps prepare students for not only continuing their education after high school and, more importantly, for life. Kamal notes that students who are accepted into his program spend more than 1,000 hours studying engineering, including a lot of fabrication in class and as part of the after-school robotics club. Read
Waterjet Case Study: The complete package
Montreal packaging solutions manufacturer continuously invests in automation to keep pace with growth and keep its R&D on point Read
Videos
Using OMAX precision to build OMAX power
At OMAX, we don’t just manufacture world-class waterjet cutting systems—we rely on them every day to build the very machines our customers trust. From precision-cut brackets to custom enclosures and intricate internal components, our own waterjets are integral to our production process. Why? Because we believe in the power of our technology. Read
How easy is IntelliMAX XData
The OMAX IntelliMAX software has a powerful tool in its XData commands. Using XData is surprisingly easy to use, too, with only a few clicks needed to change settings on cutting paths. Read
The OMAX IntelliMAX Saw Function can save you time and inventory space
The OMAX IntelliMAX Saw Function lets you easily program a straight line cut to quickly trim material to shape or remove scrap skeletons. Read