Tips & Tricks
Maintain Water Quality and Temperature for Waterjet Machine Longevity
Two factors to consider for longevity and performance of your OMAX abrasive waterjet are clean water and proper water temperature. Both environmental elements directly impact the life of your machine’s internal components and, ultimately, its performance.
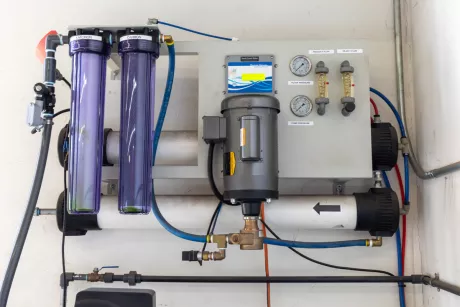
Regardless of the source – municipal or well-supplied – water quality and chemistry vary from region to region. While water chemistry does not affect a waterjet’s cutting performance, minerals such as iron and calcium along with total dissolved solids (TDS) in the water can deteriorate a machine’s pumps, seals and plumbing, leading to increased maintenance, costly rebuilds and lost productivity. To prevent these issues, it’s critical to test your water prior to implementing a waterjet in your operation and continue to monitor the chemistry and quality of your water throughout your machine’s life cycle.
As with any machine, some preventive maintenance is required – including routine water treatment. Filtration and water softeners solve many inlet water issues, and in areas where TDS exceeds 250 ppm, reverse osmosis systems can remove up to 90 percent of the solids for pure, clean water supply into the equipment.
The cost-benefit analysis for water treatment is simple: Clean water equals longer machine life with decreased maintenance costs and less downtime, leading to increased productivity.
Equally as important as inlet water quality is the content of overflow or drain water produced by the cutting process. Knowing your drain water contents, as well as understanding local and national environmental regulations pertaining to draining and discharge, are necessary to avoid the adverse consequences of draining the wrong materials.
To mitigate or correct water drainage issues, laminar flow filters remove garnet and stock material particulates, allowing them to be collected, bagged and disposed. When cutting toxic materials, your operation may require a complete water recycling solution to avoid draining toxins and other contaminants. Water recycling is the most effective way to capture toxic particles and return water to the proper specifications.
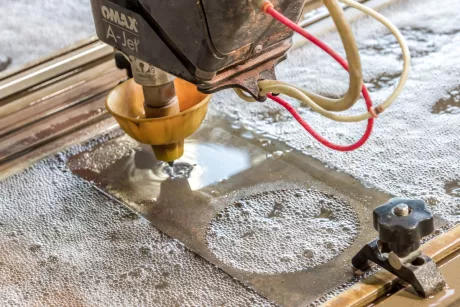
When setting up an abrasive waterjet machine, you also need to consider the location of the equipment relative to internal inbound water supply and drainage points to avoid adding increased pumping capacity and power requirements.
In addition to water quality, abrasive waterjet machines require consistent water temperatures within a moderate range to maintain high performance. OMAX recommends water temperatures not exceeding 70° F (21° C). For shops pulling inlet water through lines exposed to sun or other heat sources, high-side temperature excursions risk damage to waterjet seals and high-pressure lines, decreasing internal component longevity and increasing machine maintenance and downtime. Installing a chiller system can help maintain constant water temperature where excessive heat is an issue.
Ultimately, an efficient and durable abrasive waterjet operation begins and ends with water – its quality, contents, chemistry and temperature. Stay on top of your water to ensure performance, long machine life and regulatory compliance.