Tips & Tricks
Top 5 "Secrets" to Get More Done with Abrasive Waterjets
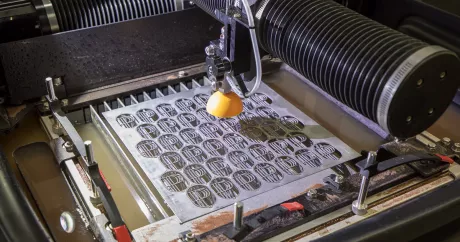
Do you know how much an abrasive waterjet can do? If you're like many of our waterjet owners & operators, you'll be surprised at the productivity these machines can add to your shop's workflow and capabilities. That's because many manufacturers who've already integrated abrasive waterjet may not take full advantage of what the technology can offer, including these five best-kept secrets of production success.
Beyond flat parts
Break out of the two-dimensional world and cut complex 5-axis 3D parts, bevels, chamfers, countersinks, crosscuts, weld-ready edges, and much more. Part geometry and complexity require finesse and a well-designed matchup between software and hardware, not mere power and pressure. The OMAX A-Jet and VersaJET cutting heads produce taper-free results on materials that milling can't handle, all without secondary machining on multiple machines – and without heat-affected zones or brittle edges. Even tackle 6-axis jobs on tube, pipe and bar stock with the addition of the OMAX Rotary Axis accessory.
Easy to learn, easy to run
We built our OMAX IntelliMAX software to do three things exceptionally well: Control the unique performance parameters of our hardware; cut great parts fast; and shorten the learning curve between introduction and productivity. At a time when shops everywhere struggle to find skilled operators, IntelliMAX makes it easy to advance from basic proficiency to confidence. We also offer virtual training for additional progress. With a full online help system built directly into the software and the ability to go from imported 3D drawing to parts in progress with just a few steps, IntelliMAX makes complex parts simple to program and cut.
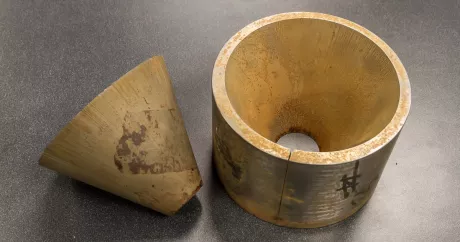
Cut the difficult stuff
You may already know that an abrasive waterjet can cut through 12"-thick metal, but do you realize just how many of today's toughest and most-challenging materials are no problem for this technology? No other cutting tool can handle everything from nickel-based hard alloys such as Inconel® and Hastelloy® to aluminum, carbon fiber, composites, copper and brass, glass, plastics, stone and titanium, as well as steels and stainless steels. No more worries about tool life, fumes, melted parts, frayed or delaminated edges, burrs or burn marks.
Take it with you
Unlike almost all other cutting technologies, an abrasive waterjet works the same way on the small scale as it does on full-sized machines – if you choose the right machine. While others might skimp on capabilities when they try to build compact waterjets, OMAX doesn’t. When you want to incorporate the near limitless versatility of this technology for small spaces and portable use, the ProtoMAX offers you big performance in a small, castor-mounted footprint. While, it may be only 39.5" wide and 41.5" deep, this isn't a toy or a proof-of-concept machine; it's a full-featured, ready-to-run waterjet ready to build prototypes or short-run parts and work side by side with traditional machine tools. We can deliver ProtoMAX virtually anywhere in the world, including by helicopter.
Make it quick
We build our hardware to offer high-performance results, but OMAX IntelliMAX software makes one of the biggest contributions to the speed and quality of our abrasive waterjet cutting. Our current fourth-generation software builds on computational research and real-world data to significantly increase cutting speeds with complex path geometries while maintaining consistent cut quality.
That advancement draws on continuous, ongoing software research and development, including countless hours spent gathering data about the behavior of the abrasive jet itself. And because every OMAX customer receives lifetime software updates, your machine always benefits from our latest optimizations to enhance the speed and quality of your cuts.
With an OMAX abrasive waterjet in your shop, you can get more done in less time and with better results than you ever thought possible. We build and support all our technology right here in Kent, Washington – and we're ready to help you put the secrets of waterjet cutting to work for you.