Tips & Tricks
Is Your Shop Ready for a Boom in Infrastructure Megaprojects?
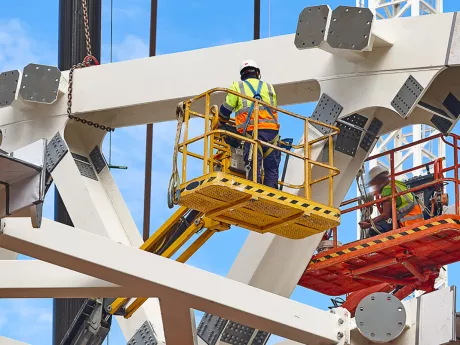
The US is joining the rest of the world with a huge investment in infrastructure construction that will see major jobs across the country for years to come. Large contracting companies are getting ready for these large projects, and waterjet technology will be one of the foremost machining tools utilized to accelerate production timelines.
Bridge construction and retrofits, water infrastructure projects, mass transit improvements, road repair and broadband expansion are all on the menu, and there’s plenty of room at the table for job shops, if they’re ready. Large contractors and enterprise firms taking on the major scope of these megaprojects will be looking for support and outsourcing an untold amount of component and part fabrication, much of which falls directly in the wheelhouse of abrasive waterjet cutting capabilities.
Because waterjets are, in fact, material neutral, they can cut virtually anything from hardened tool steel and titanium to glass, composites, plastics and rubber with no tooling changes. That versatility can’t be found with other machining methods. Additionally, waterjet cutting is a cold-cut process that eliminates heat affected zones, burn marks and burring. Unlike traditional CNC machines, waterjets do not suffer from tool wear, meaning tolerances are consistent and production is constant. Though most waterjet cutting is done on materials that are three inches thick or less, waterjets are capable of cutting through a foot of most materials by adjusting the machine’s cutting speed.
With the enormous flexibility and capability found in one machine, many job shops are complementing their other manufacturing processes with abrasive waterjets to expand their customer base and keep many applications in house that would otherwise be outsourced. With hundreds of thousands of new manufacturing and construction jobs looming on the horizon, large contractors and OEMs will soon be looking for shops that can handle specialized manufacturing requests and fill orders fast. Now is the time for shops to expand and build out their capabilities.
The vast amount of work and jobs expected to be created by the investment act are both a boon and a bane to the manufacturing industry. The current shortage of skilled workers plaguing today’s shops could only be exacerbated, making it more necessary than ever to automate production. The user-friendly design features incorporated into OMAX systems will allow shops to maintain production in light of the current labor force challenges.
Also, OptiMAX and MAXIEM waterjet machines are scalable with options that will allow shops to expand the types of parts they can process and jobs they can take on. The ability to increase capability and complexity in the future allows shops to cost-effectively acquire a waterjet machine today with the ability to easily pivot to the needs of the future.
Contact us to learn how a waterjet can improve how you run operations