Customer Success: Manufacturing
Trupart Builds on a History of Manufacturing Innovation
Machine: OMAX 2652

“In 2001, my grandfather noticed a huge dip in stamping, most of it being outsourced overseas,” said Shane Prukop, president of Trupart Manufacturing Inc. “In an effort to offer other services, we purchased our first abrasive waterjet machining system. It opened a whole new world and laid the groundwork for what we can manufacture now. The OMAX helped fill a gap.”
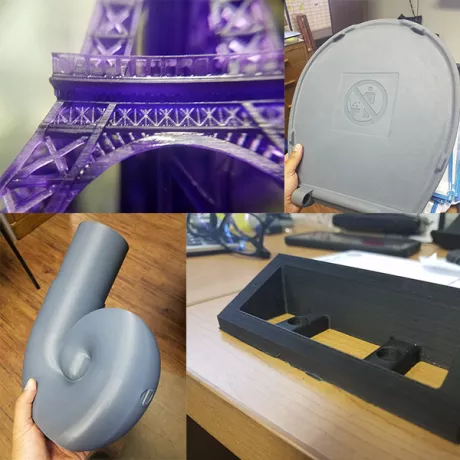
With its state-of-the-art equipment – including lasers, 3D printers, and an OMAX abrasive waterjet – Trupart Manufacturing can fabricate components with nearly any material, no matter their shape or design. “Our shop cuts a wide variety of thicknesses and materials. Tungsten, titanium, steel, aluminum, ceramic, glass, plastic, rubber, foam, wood, and even the oddballs like speakers, connectors, computers and other random stuff our customers ask for,” said Prukop. “These machines can cut everything!!” It’s this combination of next-level machining technologies that allows Trupart to succeed, a set of manufacturing capabilities Prukop assembled with an eye toward investing in innovation.
The family’s manufacturing lineage goes back 45 years to Prukop’s grandfather, Karl Schlosser, who operated classic stamping machines via the company he founded in 1973, Tricoss Inc. Trupart Manufacturing originally grew out of Schlosser’s company after Prukop was tasked with picking up odd jobs for the shop’s waterjet. Prukop quickly found that he could start his own business with the fabrication skills he learned at Tricoss, and when Prukop’s grandfather retired, Prukop purchased the business and folded it into the rapidly growing Trupart Manufacturing.
Over the years, both Tricoss and Trupart have owned several OMAX waterjets, trading them in for larger units as the companies’ need for cutting capacities grew. Currently, Trupart uses an OMAX 80X JetMachining Center with a cutting envelope of 13'4" by 6'8". This robust and reliable system requires little maintenance and maximizes both machining time and profit margins. The 80X is ideal for cutting larger or multi-part projects, and thanks to its substantial cutting bed capacity, there aren’t many jobs that Trupart can’t fit under the jet. And since the large waterjet uses a cold-cutting process, it can cut nearly any material without creating the heat-affected zones or material distortion that can be caused by such processes as laser and plasma machining.
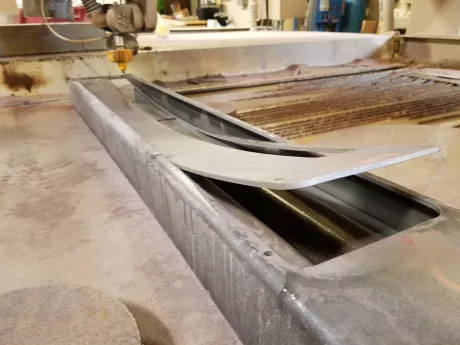
“One thing we realized early on about abrasive machining is that it's quite simple. The IntelliMax 2D CAD software is genius. From there to pathing the part is really simple, and we can usually train people in a week,” Prukop explained. “Adding an abrasive machining center not only allowed us to make parts quickly with no tooling but opened up a whole world of hard-to-cut materials and geometries that once were impossible with our other in-house equipment. It helped big time on producing fixtures and other random components the shop needed to get other jobs done. Simple routine maintenance can keep issues at bay and keep the machine cutting 24/7. If we do have a problem though, OMAX is right there with excellent support and parts the next day.”
Additive manufacturing processes and abrasive waterjet are ideal complements to each other in a fabrication space. “Together, they can streamline the process through prototype, production and quality control,” said Prukop. “Printing parts like jigs gives us a competitive edge. We also use printed parts as go/no-go gauges for final quality control of components to ensure they match the final specs after processes such as forming welding or insert install.”
Four decades of experience has shown Trupart what it takes to stay ahead of the manufacturing game. A gift for making smart choices about machinery has given Prukop an edge on his competition, and with an OMAX waterjet to complete Trupart’s workflow, the manufacturing industry should expect to hear more and more from this fabrication enterprise.
“Being able to produce parts quickly and accurately are very important in the world of just-in-time manufacturing,” said Prukop. “Sometimes people need stuff quick, and the waterjet can perform that task well!”