SEE IN PERSON
The OMAX OptiMAX 60X is the culmination of three decades of engineering expertise and experience, resulting in the world’s most advanced waterjet.
- Cutting envelope of 10' x 5’ 2” (3.04 m x 1.57 m)
- ±0.001" (±0.025 mm) linear position accuracy
- Backed by our exclusive IntelliMAX Premium Software
- Exclusive IntelliTRAX abrasive jet linear drive system provides 350 in/min (8.9 m/min) traverse with real-time closed-loop positioning feedback
- 12-inch (305 mm) programmable Z axis travel with lowest ceiling height requirement design in the industry.
- Standard Rapid Water Level Control for cleaner, safer, and quieter submerged cutting completes most work below 80 dBA
- Does not create heat-affected zones or mechanical stresses
- Machines a wide range of materials and thicknesses, from metals and composites to glass and plastics
- No tool changes & minimal fixturing dramatically reduce setup
- Unlimited free training for the life of your machine
- Unlimited software upgrades for the life of the machine
- 2-year / 4000-hour limited warranty
- 3 days of onsite training upon installation
DIMENSIONS & SPECS
Footprint (with pump & controller) | 22' 8" x 11' 11" (6.91 m x 3.63 m) |
---|---|
Height (with Scissor plumbing) | 9' 9" (2.97 m) |
Operating Weight | 36,118 lb (16,383 kg) |
Weight (tank empty) | 8,500 lb (3,855 kg) |
X-Y Cutting Travel* | 10' x 5' 2" (3.04 m x 1.57 m) |
Z-Axis Travel (with Motorized Z Axis)* | 12" (304 mm) |
Table Size | 12' 6" x 6' 2" (3.81 m x 1.88 m) |
Material Supports Slats | 4" x 1/8" Galvanized Steel |
---|---|
Maximum Supported Material Load | 400 lbs/sq ft (1,950 kg/sq meter) |
Electrical Requirements | 3-Phase, 380-480 VAC ±10%, 50-60 Hz |
Noise Level | Below 80 dBA at one meter for submerged cutting |
Speed | 350 in/min (8.89 m/min) |
Linear Positional Accuracy* | ±0.001" (±0.025 mm) |
Repeatability* | ±0.001" (±0.025 mm) |
Ballbar Circularity* | ±0.003" (±0.076 mm) |
* Accessories may reduce travel. Accuracy specifications are at 72° F (22° C).
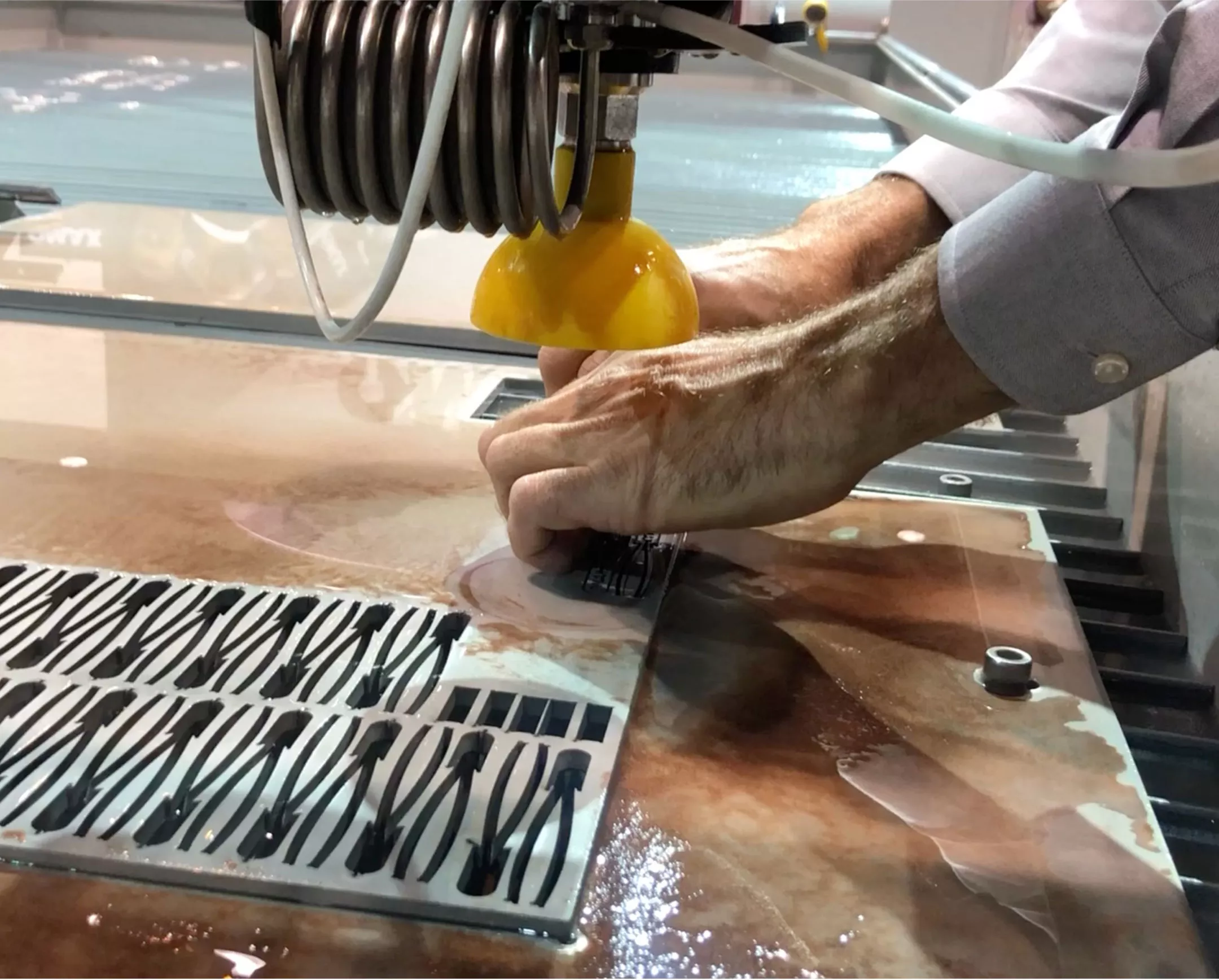
PUMP INFO
Maximized uptime with 1,000 hours between maintenance cycles
Increased production by delivering 30% more cutting power
Variable Frequency Drive reduces startup power consumption and maximizes operating flexibility
EnduroMAX 100 HP | EnduroMAX 50 HP | EnduroMAX 30 HP | DynaMAX 330 | |
---|---|---|---|---|
Motor Power | 100 HP (75 kW) | 50 HP (37kW) | 30 HP (22 kW) | 30 HP (22 kW) |
MAX Jet Power | 85 HP (63 kW) | 42.5 HP (31.5 kW) | 25.5 HP (18.7 kW) | 20.6 HP (15.1 kW) |
Output Pressure | 60,000 psi | 60,000 psi | 60,000 psi | 60,000 psi |
Orifice & Flow Rate ** | 0.022" / 2.25 gpm (0.56 mm / 8.52 lpm) |
0.016" / 1.20 gpm (0.41 mm / 4.54 lpm) |
0.012" / 0.67 gpm (0.30 mm / 2.54 lpm) |
0.014" / 1.0 gpm (0.35 mm / 3.8 lpm) |
Footprint LxWxH | 44" x 62" x 44" (1,118 mm x 1,575 mm x 1,118 mm) |
66" x 36" x 38.5" (1,676mm x 914mm x 978mm) |
66" x 36" x 38.5" (1,676mm x 914mm x 978mm |
43" x 53" x 40" (1090 mm x 1350 mm x 1010 mm) |
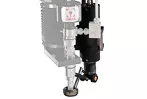
Collision Sensing Terrain Follower
The Collision Sensing Terrain Follower is an essential tool for working with uneven surfaces.
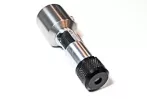
Laser Feature Finder
The Laser Feature Finder allows for visual reference before introducing water and garnet.
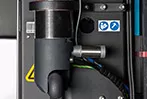
Automated Air Sweep
In the event of a nozzle clog, the automated Air Sweep is designed with a fluid diverter to direct water away from the abrasive hopper.
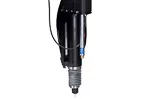
OMAX Drill Head
Achieve reliable piercing of composites and laminates with an OMAX-Engineered pneumatic drill.
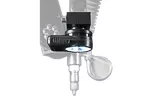
Precision Optical Locator
The Precision Optical Locator is designed to let you accurately place parts on the OMAX for secondary machining operations.
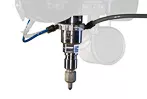
Vacuum Assist
The OMAX Vacuum Assist is ideal for piercing brittle materials, advanced composites, challenging laminates, and more.
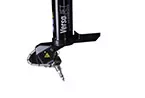
VersaJet
VersaJET has a cutting range of 0 to 60 degrees for cutting beveled edges, angled sides, countersinks and complex 3D shapes.
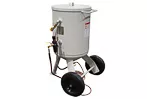
Bulk Abrasive Delivery System
Available in 100lbs., 600lbs., 2200 lbs. and 170 L systems, the Bulk Abrasive Deliver Systems provides continuous pressurized garnet.
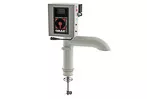
Variable Speed Solid Removal System
The Variable Speed Solid Removal System allows for controlled solid evacuation to reduce downtime.
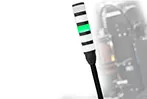
Machine Status Indicator
Decrease operator observation and increase productivity with the machine status indicator lights for OptiMAX.
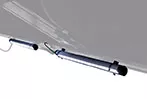
Under Bridge Lighting
Direct illumination of the cutting surface allows for the operator to clearly see the nozzle location, with two LED light banks to aid in cut set up, visibility, and project completion.
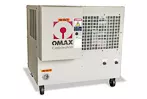
Chiller System
OMAX Chiller supplies inlet water at a consistent temperature extending pump seal life for longer, sustainable production.
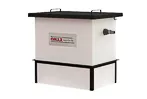
Laminar Filter
The Laminar Filter cleans overflow required for recycling through a closed loop system or for sanitary disposal.
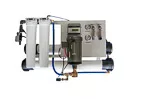
Reverse Osmosis System
The Reverse Osmosis System can remove 90% of total dissolved solid in water.

Water Recycling System
The OMAX Water Recycling System captures and reuses workable overflow water.
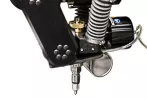
TiltaJet
The TiltaJet lets the OMAX JetMachining Center achieve virtually zero taper.
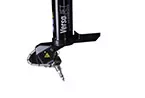
VersaJet
VersaJET has a cutting range of 0 to 60 degrees for cutting beveled edges, angled sides, countersinks and complex 3D shapes.
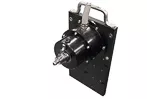
Rotary
The Rotary Axis is a submersible rotary head that allows the abrasive waterjet to cut up to 6-axis paths to create complex 3D shapes in tube, pipe, and bar stock.