Tips & Tricks
Waterjet Myths Uncovered – Thick Material
Myth:
Waterjets are only good for cutting thin materials.
Fact:
Modern waterjet systems are optimized to cut materials between ¼ inch up to 3 inches thick. Given enough time and consideration for taper, waterjets can cut as thick as you want.
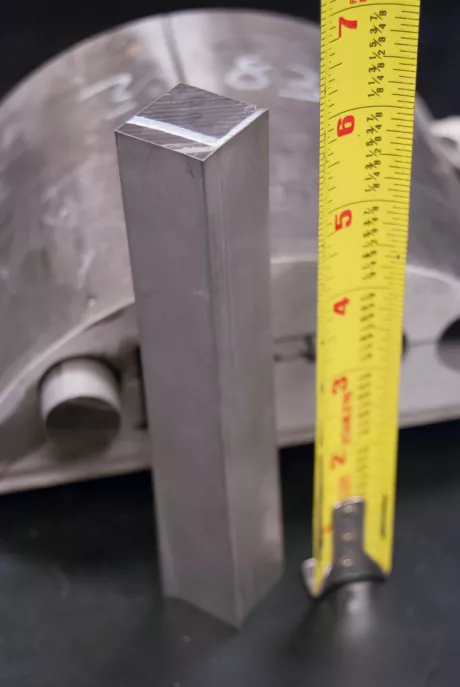
Maintaining Control
Since water wants to return to its natural state, the jet will degrade and begin to thicken so it is narrower at the top and thicker at the bottom. The thicker the material, the more control and understanding of the jet is required. Jet stabilization is key for cutting thicker materials.
There are several factors that allow for the control and stabilization of the stream of water and garnet to cut thick, dense materials with precision. These factors include software, hardware and the material itself
Software
Software designed specifically for waterjet cutting, such as OMAX’s IntelliMAX Software Suite, will perform better than software designed only for motion control since a waterjet is a soft, reactive tool compared to traditional hard, rigid tool tips. IntelliMAX’s predictive model calculates the motion of the jet to navigate the material type, thickness and geometry and adjusts the speed to minimize the natural taper and spread.
Once the software calculates how the jet will perform in a given material, it will transfer the information to the hardware for speed and motion for optimal cutting and control.
Hardware
The hardware installed on your waterjet assists the software in cutting thicker materials with speed and precision. From the linear drive system to the cutting head, the system components work together to even out the jetstream and ensure the commands of the software are followed.
Articulating cutting heads tilt forward to increase the jet’s cutting speed and balance so it has less lag and angle left to right to put the taper into the scrape side of the material. The part geometry, material density and thickness will determine how much compensation will be needed by the cutting head.
The motion control system provides an accurate location on the table and ensures proper speed to maintain a proper jet.
Maintenance of your hardware components will ensure your best jet and allow the software to do its job.
Material
The material itself plays an important role in stabilizing the jet. In abrasive waterjet cutting, the material acts as an extension of the tool tip. Once the material catches the jet, the jet begins to stabilize. Thicker material allows for more time for the waterjet to stabilize. Denser materials also hold the jet better and allow for more stabilization.
To ensure you have a good, stable stream going into your material, you must have a proper stand-off. The recommended stand-off based on your nozzle and mixing tube combination should always be followed for the best jet quality. Too high of a stand-off and you will have poor edge quality and a less stable jet; too close and you will risk nozzle clogs.
The longer you can keep the jet stable, the thicker you can cut. Modern waterjet systems use a combination of hardware and software components to assist in predicting the optimal jet. Dense and /or thick materials also play a role in keeping the jet consistent and stable compared to thinner materials and can be more efficiently cut on waterjet.