Tips & Tricks
What Is A Cutting Model?
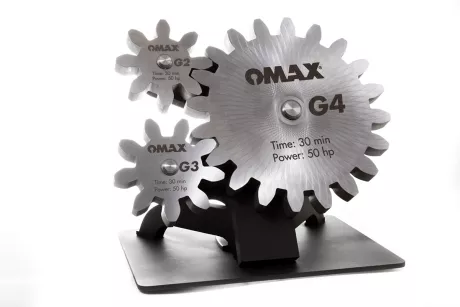
The abrasive waterjet cutting model is, perhaps, the most significant factor in propelling abrasive waterjets into mainstream manufacturing. Advancements in the OMAX cutting model have decreased part production times, increased cutting precision, and made OMAX abrasive waterjets very easy to program. Yet, there’s not much discussion about what a cutting model is, or what it does. This is probably due to the fact that it’s “behind the scenes” and isn’t something an OMAX waterjet operator needs to understand, or even know about.
The cutting model uses sophisticated mathematical modeling to predict the precise motion and shape of the jet stream along each entity of a tool path based on the operating parameters. The cutting tool on an abrasive waterjet is a high-velocity stream of water and abrasive, known as the jet stream. Unlike rigid cutting tools, such as a tool on a CNC mill, the jet stream is a “floppy” tool that bends as it cuts, and the shape of the stream changes depending on how fast it’s moved. This means that a waterjet will tend to undercut corners and swing wide on curves if it’s moved like a traditional, rigid cutting tool. The jet stream will react differently when cutting different material types, different thicknesses and at different speeds. In order to produce precision parts in a cost-efficient manner, motion control system must compensate for the behavior of the jet stream.
Early versions of waterjets required a lot of trial and error and a skilled programmer to adjust the jet motion to produce accurate parts. Now, advanced waterjets use cutting models that automatically predict the behavior of the jet stream and make adjustments to compensate for that behavior. With OMAX waterjets, a machine operator simply enters the material type, thickness and desired edge quality, and for the given part file, the OMAX machine controller automatically determines and sets the optimal speed and path the cutting head will move along to cut a high tolerance part in the least amount of time. There’s no trial and error and no need for a skilled programmer because all the experience and knowledge is built into the controller.
Some water jets cutters rely on cutting models that are built into the CAD/CAM or nesting software. In such cases, the part tolerance and overall cutting time will vary when using different CAD/CAM programs or nesting software to program the tool path. The OMAX cutting model, however, is built right into the machine controller. This means that no matter what CAD/CAM or nesting software you use to program the tool path on your OMAX waterjet, your part will be cut with the same high tolerance and in the same amount of time every time. And since the OMAX 4th generation cutting model is the most advanced abrasive waterjet cutting model in the world, in most cases cutting on the OMAX will result in more accurate parts in less time than when cutting on other waterjets.
Some waterjet manufacturers have no cutting model and no automation for setting the optimal cutting speeds. Other manufacturers rely on data published by universities and other public sources to build their cutting models. At OMAX, we have an in-house team researching, developing and continuously improving our cutting model, enabling our customers to cut complex parts with tight tolerances in the least amount of time. The image with this article visually demonstrates how much the cutting model affects cutting time. Each of the gears in the image were cut on the same machine, from the same material, with the same hp pump, in the same amount of time. You can see how the 3rd generation (G3) cutting model cut more than the 2nd generation (G2) in the same amount of time, and the 4th generation (G4) cutting model cut significantly more than the 3rd generation.