News Articles
Excerpt from MetalForming
Fundamentals of Waterjet Cutting: Optimum Efficiency
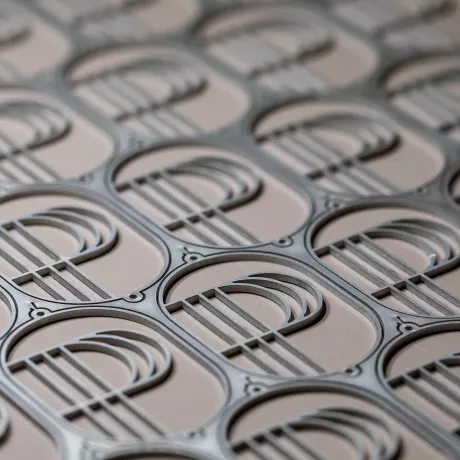
While most users of abrasive waterjet cutting profess its ease of use, anyone that owns a waterjet will admit that while cutting a one-off part might be easy, producing thousands of the same part, with 0.05-in. tolerance, requires knowledge and skill. The difference comes down to understanding process fundamentals and how they work together. Let’s examine a few fundamental tips to help metal formers optimize day-to-day efficiency with their abrasive waterjet cutting machines. These tips apply to all users, and while some may seem rudimentary, what ultimately separates novices from advanced users is a thorough understanding of the process.
Abrasives
As far as cost savings and efficiency goes, there are few skills better to learn then how to manage your abrasive. Operators of waterjet cutting machines should set the rate of garnet flow based on the size of the machine’s nozzle orifice and the mixing-tube diameter. Using excess garnet only wastes money, and the mixing tube will not be able to handle the volume; too little garnet will impact separation speed, resulting in inefficient cutting and adding hours to the job time. Often, the higher the flow rate, the quicker the separation speed. This sounds counter-intuitive, as shops seek efficient use of consumables, but the key is to assume greater control over separation speed. Instead, operators should seek out the sweet spot of garnet flow, achieving optimum separation speed with the correct finish while only using the necessary amount of abrasive.