Customer Success: Manufacturing
Waterjeting in Waikite Valley With Jemco Manufacturing
Machine: GlobalMAX 1530
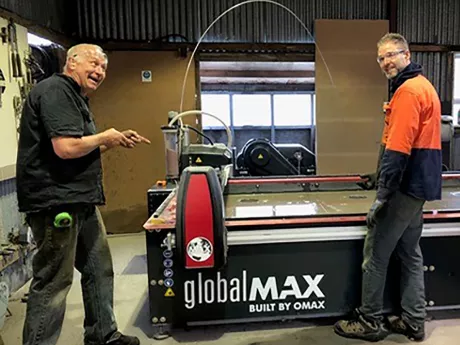
Jemco Manufacturing has been producing metal works in Waikite Valley, New Zealand, since 2009. “We started with a development of a product for our own use and, through popular demand, created a business from this initial product,” said Mary Simons, managing director of Jemco Manufacturing. The rural, five-person, customer-focused shop specializes in farming, automotive, and prototyping for customers across New Zealand.
As Jemco grew its customer base, the company streamlined their manufacturing operations to accommodate the new business. As Simons explained, “We wanted a machine that had the ability to cut a range of materials accurately with a good finish. After investigating the other options on the market, we decided a waterjet cutter fit the best with our needs.”
In June 2019, Jemco installed a GlobalMAX 1530 with a 30 hp pump. A value-focused abrasive waterjet, the GlobalMAX 1530 can cut almost any material and a wide variety of thicknesses without creating heat-affected zones. The economical machine does X/Y-axis cutting with three degrees of freedom and has several compatible accessories, including a terrain follower, a pneumatic drill and bulk garnet feed hopper.
“The OMAX training that we received from the New Zealand OMAX agents, Roadrunner Manufacturing, has been absolutely superb,” said Simons. “The training and backup is one of the reasons that we chose OMAX, and it has exceeded expectations.” Roadrunner is a manufacturing entity in its own right, but they also serve as the exclusive distributor of OMAX brand products in New Zealand. In this capacity, Roadrunner’s dedication to their end users is excellent and their attention to customer service remains unmatched.
For years, Jemco’s signature item has been the “Smokey Goat” topper. The all-terrain pull-behind is an industrial-scale lawn mower used for keeping large grass areas tidy, and the adjustable horticultural wheel allows users to maneuver close to fence lines and posts. Much of the Smokey Goat’s fabrication has been transferred to the GlobalMAX since Jemco installed the machine. According to Simons, the waterjet now handles all of the bodies, tow bar plates and anti-skid plates, and when the company prototyped its horticultural model, it used the waterjet to produce the back-wheel structure.
Like other fabricators, Jemco has found that the benefits of an in-house waterjet allows for quicker turnarounds and on-demand precision. “Bringing all our mainstream cutting in-house has given us the ability to quickly and easily produce products on our timeline,” said Simons. “We mainly cut steel, stainless, aluminum and high-molecular-weight polymers ranging from two to 12 millimeters. Being able to have an idea, draw it up and make it, especially in the prototype stage, work both for our products and our clients.”
Jemco is also the exclusive supplier of Plaztuff™ High Molecular Weight Polymer sheets for the South Wiakato and Bay of Plenty Regions, which the company uses to produce custom orders such as truck bed liners and light-weight tankage for farm use in addition to selling wholesale. Since abrasive waterjets cut nearly any material available, the Plaztuff is just as easy to machine as anything else, or, as Simons puts it, “The waterjet breezed through it.”
“The extra components that we now cut with the waterjet instead of hand producing has increased our production ability tremendously,” said Simons, who expressed excitement about the company’s expansion into other manufacturing areas thanks to the power of the GlobalMAX 1530. “The options of what we can do and offer now have opened new markets.”