Z-Axis Accessories
Motorized Z-Axis
The electrically operated OMAX Motorized Z-Axis provides precise nozzle positioning. The powerful combination of the Motorized Z-Axis and the Precision Optical Locator provides precision jet machining of pre-machined parts, such as die-stripper plates.
Available on these machines:
GlobalMAX 1508, GlobalMAX 1530, GlobalMAX 2040, MAXIEM 1515, MAXIEM 1530, MAXIEM 2030, MAXIEM 2040, MAXIEM 2060, MAXIEM 2080, MAXIEM 3060, OMAX 2626, OMAX 2652, OMAX 5555, OMAX 60120, OMAX 55100, OMAX 80X, OMAX 120X Series, OMAX 160X, OptiMAX 60X, OptiMAX 80X Series
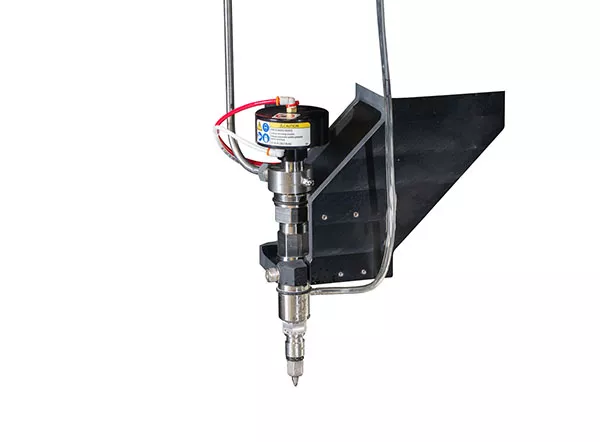
Features
- Simple setup and operation
- Automatically maintains the correct nozzle standoff throughout the cutting process
- Adjusts automatically to uneven surfaces; reduces need for additional programming
- Constantly senses necessary height adjustments when activated, unlike other contour following products on the market
- Reduces potential equipment damage from nozzle collisions
- No special programming required
- No requirement to map the elevation of your material - simply move the nozzle to where you want to begin cutting and push start
- Electrical connections armored for durability
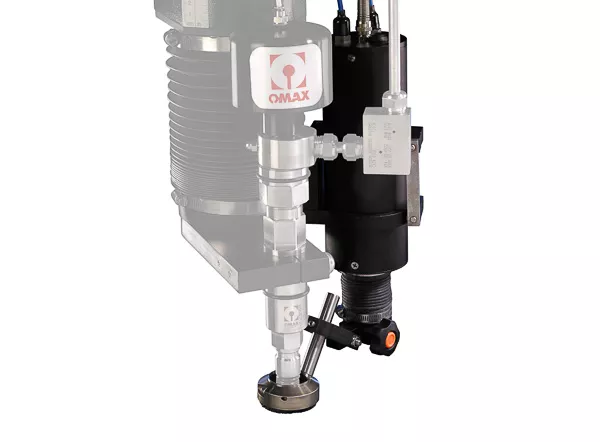
Collision Sensing Terrain Follower
The Collision Sensing Terrain Follower is an essential tool for working with uneven surfaces. The innovative design allows you to set the machine standoff once at the start and then the Collision Sensing Terrain Follower constantly and continuously compensates for material height changes to maintain precise standoff. In addition to maintaining precise standoff.
Available on these machines:
GlobalMAX 1508, GlobalMAX 1530, GlobalMAX 2040, MAXIEM 1515, MAXIEM 1530, MAXIEM 2030, MAXIEM 2040, MAXIEM 2060, MAXIEM 2080, MAXIEM 3060, OMAX 2626, OMAX 2652, OMAX 5555, OMAX 55100, OMAX 60120, OMAX 80X, OMAX 120X Series, OMAX 160X, OptiMAX 60X, OptiMAX 80X Series
Contact Sales
Features
- Simple setup and operation
- Automatically maintains the correct nozzle standoff throughout the cutting process
- Adjusts automatically to uneven surfaces; reduces need for additional programming
- Constantly senses necessary height adjustments when activated, unlike other contour following products on the market
- Reduces potential equipment damage from nozzle collisions
- No special programming required
- No requirement to map the elevation of your material—simply move the nozzle to where you want to begin cutting and push start
- Electrical connections armored for durability
Drill
Solely customized for OMAX machining, the robust Drill permits repeatable piercing of laminates and composites prior to abrasive waterjet cutting and accurately pierces small diameter holes in thick material. With IntelliMAX innovation, no separate programming is required.
Available on these machines:
GlobalMAX 1508, GlobalMAX 1530, GlobalMAX 2040, MAXIEM 1515, MAXIEM 1530, MAXIEM 2030, MAXIEM 2040, MAXIEM 2060, MAXIEM 2080, MAXIEM 3060, OMAX 2652, OMAX 2652, OMAX 5555, OMAX 55100, OMAX 60120, OMAX 80X, OMAX 120X Series, OMAX 160X, OptiMAX 60X, OptiMAX 80X Series
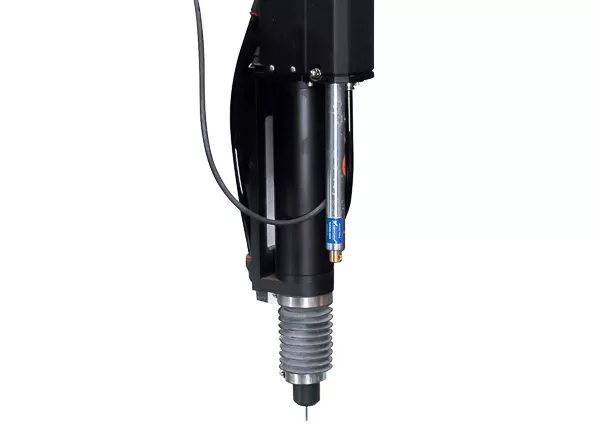
Features
- Successfully pre-drill brittle and sensitive materials
- Corrosion-resistant cylinder wall will not rust in moist air
- 5,000 RPM air motor provides maximum power
- Drill equipped with a collet holder and collet to hold a 1/16" (1.5 mm) drill bit
- Fully adjustable pneumatic feed rate and depth of feed up to 3" (76 mm) of travel and 112 lbs (7.7 bar) of thrust with 85 psi air
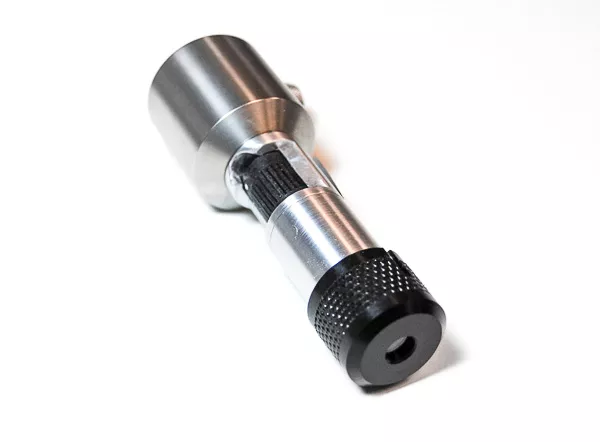
Laser Feature Finder
The Laser Feature Finder helps to perform simple dry runs with this laser attached to the nozzle before you cut parts on valuable stock. Get a rough visual reference of where your jet stream will begin cutting by locating material features without special software.
Available on these machines:
GlobalMAX 1508, GlobalMAX 1530, GlobalMAX 2040, MAXIEM 1515, MAXIEM 1530, MAXIEM 2030, MAXIEM 2040, MAXIEM 2060, MAXIEM 2080, MAXIEM 3060, OMAX 2626, OMAX 2652, OMAX 5555, OMAX 55100, OMAX 60120, OMAX 80X, OMAX 120X Series, OMAX 160X, OMAX MicroMAX, OptiMAX 60X, OptiMAX 80X Series
Contact Sales
Features
- Includes a polarized lens to adjust the diameter of the laser dot to focus on any size material feature
- With its simple design, the accessory operates on three A76 batteries, eliminating wiring or cabling
- Easy to use
- Assists in finding tiny details on your material stock
- Promotes the ability to get the best yield out of materials
Precision Optical Locator
The Precision Optical Locator (POL) facilitates precision JetMachining of pre-machined components. The POL uses modern compact video technology to precisely locate any points, edges, or holes on a pre-machined piece of material that is placed on the OMAX cutting table. The software package then reorients the cutting program to precisely align with the located features.
Available on these machines:
OMAX 2626, OMAX 2652, OMAX 5555, OMAX 55100, OMAX 60120, OMAX 80X, OMAX 120X Series, OMAX 160X, OMAX MicroMAX, OptiMAX 60X, OptiMAX 80X Series
Contact Sales
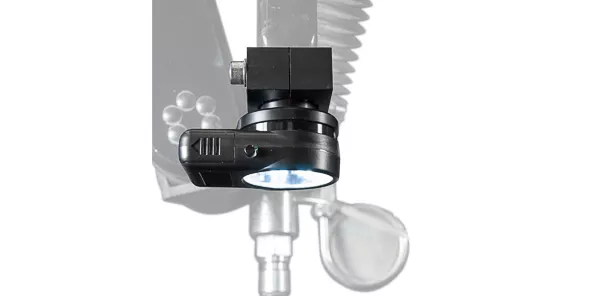
Features
- Video monitoring and software functions measure the location of material features to prepare for secondary machining, such as drilling in the center of a disk
- Video image of featured location can be saved for quality control records
- Light ring illuminates viewing area
- Includes two camera tripods, a 250-inch ethernet cable, and a sturdy accessory carrying case
- Camera resolution up to 2592 x 1944 pixels
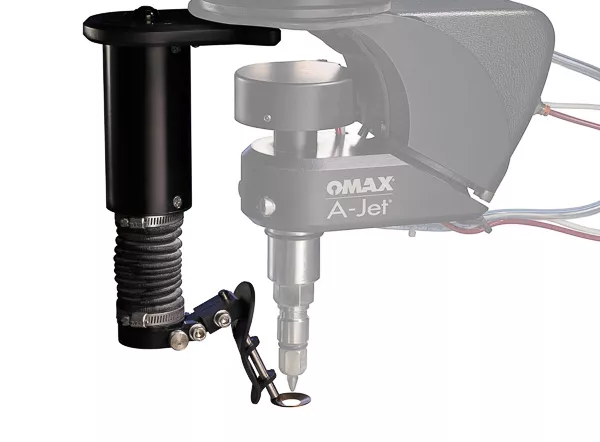
Terrain Follower
The Terrain Follower attaches directly to the A-Jet and VersaJet. Changes in a material's height are detected and the nozzle automatically makes the required height adjustments, maintaining the necessary nozzle standoff to avoid collision with warped surfaces and protecting the nozzle and related hardware from damage.
Available on these machines:
MAXIEM 1515, MAXIEM 1530, MAXIEM 2030, MAXIEM 2040, MAXIEM 2060, MAXIEM 2080, MAXIEM 3060, OMAX 2652, OMAX 5555, OMAX 55100, OMAX 60120, OMAX 80X, OMAX 120X Series, OMAX 160X, OptiMAX 60X, OptiMAX 80X Series
Contact Sales
Features
- High resolution magnetic encoder senses change in material height
- All electrical cabling is shielded from the abrasive waterjet environment
- No special programming required
- Designed specifically to operate in an abrasive waterjet environment
- Completely retrofittable to all existing A-Jet accessories
Vacuum Assist
The OMAX Vacuum Assist is ideal for piercing brittle materials. The OMAX Vacuum Assist eliminates delay between water and garnet feed, allowing for consistent automatic piercing of composites, laminates, and other materials.
Available on these machines:
MAXIEM 1515, MAXIEM 1530, MAXIEM 2030, MAXIEM 2040, MAXIEM 2060, MAXIEM 2080, MAXIEM 3060, OMAX 2626, OMAX 2652, OMAX 5555, OMAX 55100, OMAX 60120, OMAX 80X, OMAX 120X Series, OMAX 160X, OMAX MicroMAX
Contact Sales
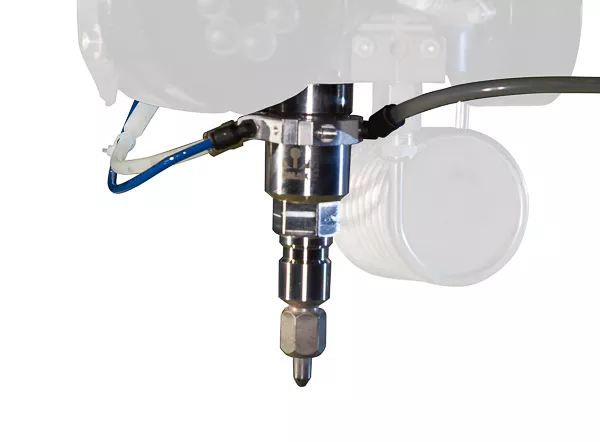
Features
- Available in a wide range of nozzle orifice sizes, from 0.007” to 0.016”, with mixing tubes from 0.015” to 0.048”
- Low-pressure stationary piercing can help improve the circularity and edge quality of small holes
- Precise on/off cycles to prevent excess garnet usage
- Automatic dynamic pressure adjustments
- Visible pressure gauge to verify correct pressure settings
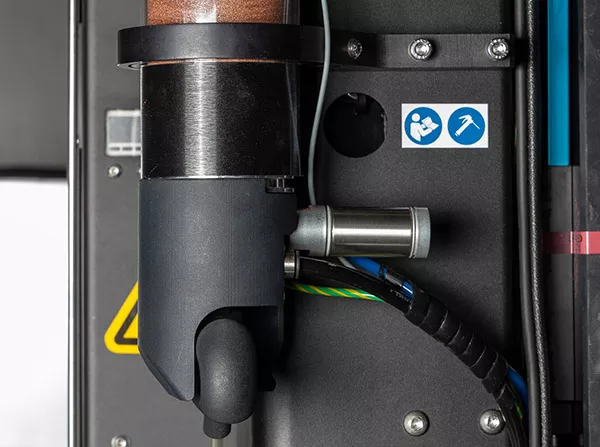
Automated Air Sweep:
The Automated Air Sweep feature on the bridge mini hopper will improve ease of maintenance and increase uptime. In the event of a nozzle clog, the automated Air Sweep is designed with a fluid diverter to direct water away from the abrasive hopper. If a clog occurs, OMAX IntelliMAX software includes a feature that purges the nozzle and abrasive feed line with air and water to clear the clog. This process eliminates the need to disassemble the nozzle and mini hopper, reducing downtime.
Available on these machines:
OptiMAX 60X, OptiMAX 80X Series
Features
- Automated process to increase uptime and avoid operator intervention
- Designed with two methods to protect and clear any potential nozzle clogs
- Fully controlled within the software
OptiMAX Vacuum Clog Sensor
The OptiMAX Vacuum Clog Sensor pairs with the IntelliMAX software to seamlessly clear a clog during a cut without requiring intervention from the waterjet operator. The Vacuum Clog Sensor will automatically detect and safely clear the clog before returning back to the location on the cutting path where the clog occurred to resume cutting.
Available on these machines:
OptiMAX 60X, OptiMAX 80X Series
Contact Sales
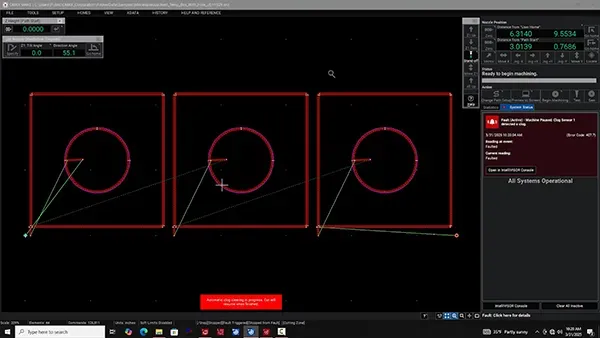
Features
- Can be retrofitted to any OptiMAX waterjet system
- The sensor can be added to the Motorized Z, TiltaJET, or VersaJET cutting head
- Communicates with OMAX IntelliVISOR to alert users in the event of a clog