
SAIBA MAIS SOBRE OS SISTEMAS DE JATO DE ÁGUA
COMO FUNCIONAM OS JATOS DE ÁGUA?
1. Bomba de alta pressão
A bomba gera um fluxo de água pressurizada para o processo de corte.
2. Cabeça de corte
Uma cabeça de corte é um requisito padrão, mas uma opção adicional aos jatos de água da OMAX, uma cabeça de corte multieixos controlada por computador permite cortes angulares e pode ser utilizada para minimizar automaticamente a conicidade para cortes verticais precisos.
3. Bocal de jato de água abrasivo
Dentro do bocal, a água pressurizada passa por um orifício de pequeno diâmetro e forma um jato de água coerente. O jato passa então por uma secção de venturi onde uma quantidade medida de abrasivo granular é atraída para a corrente de água. A mistura de água e partículas abrasivas passa através de um tubo especial de mistura em cerâmica e o abrasivo/água resultante sai do bocal como um fluxo de corte coerente de partículas abrasivas que viajam a uma velocidade muito elevada.
4. Depósito de captação
O depósito de captação cheio de água dissipa a energia do jato abrasivo depois de ter cortado o material alvo de trabalho mecânico.
5. Tremonha abrasiva
A tremonha abrasiva e o sistema de controlo do fluxo abrasivo associado fornecem um fluxo doseado de abrasivo granular ao bocal.
6. Sistema transversal X-Y
Um sistema de movimento X-Y de precisão é utilizado para mover com precisão o bocal, de forma a criar a trajetória de corte desejada.
7. Controlador baseado em PC
Os controladores de movimento avançados para sistemas de jato de água abrasivo são baseados em PC e permitem a produção de peças precisas com uma experiência mínima do operador.
MOTION CONTROL
Because the waterjet cutting medium is liquid and not static, a waterjet tends to undercut corners and swing wide on curves when moved as one would move a traditional rigid cutting tool. OMAX eliminates this issue by using an advanced computer model to accurately predict the motion and shape of the cutting stream and then by using a PC-based motion control system to compensate for undesired jet motion. The result is a fast, accurate part the first time. No trial and error and no need for an experienced programmer because the experience and the knowledge is in the control software.
BOMBAS
Os sistemas de corte por jato de água utilizam a bomba hidráulica intensificadora mais antiga e mais complexa ou a nova bomba de êmbolo triplex, mais simples, acionada por cambota. As bombas de cambota são inerentemente mais eficientes do que as bombas mais intensivas porque não requerem um sistema hidráulico de rotação de potência. A transmissão da cambota é um sistema de transmissão direta puramente mecânico com perdas por fricção mínimas, pelo que são típicas eficiências entre 85% e 90%. Isto significa que 85% ou mais da energia elétrica fornecida ao motor de transmissão pode efetivamente ser fornecida junto do bocal de corte, em comparação com os típicos 65% ou menos de uma bomba intensificadora. Historicamente, as bombas intensificadoras tinham a vantagem de uma vida útil da vedação e da válvula de retenção mais longa, mas as melhorias contínuas nos desenhos e materiais de vedação e a ampla disponibilidade e o custo reduzido dos componentes cerâmicos das válvulas permitem agora operar uma bomba de cambota na gama de 60.000 PSI (4.137 bar) com longos intervalos de manutenção e excelente fiabilidade.
A OMAX utiliza bombas de transmissão direta com cambota de alta eficiência exclusivamente para todos os seus sistemas. Uma bomba de transmissão direta é mais eficiente do que uma bomba hidráulica intensificadora tradicional e por isso pode fornecer mais potência líquida ao bocal de corte, resultando em cortes mais rápidos. É silenciosa e limpa, sem risco de fugas hidráulicas complicadas. Além disso, uma bomba de transmissão direta é simples de compreender, de solucionar problemas e de manter. A bomba EnduroMAX da OMAX dispõe de um intervalo de manutenção preventiva de 1000 horas, oferecendo o máximo em funcionamento fiável e de baixo custo.
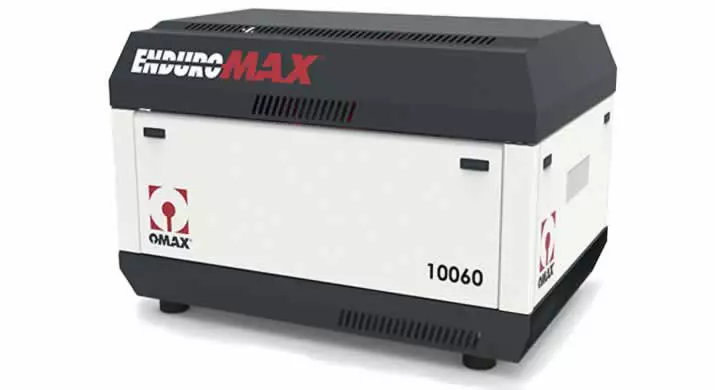
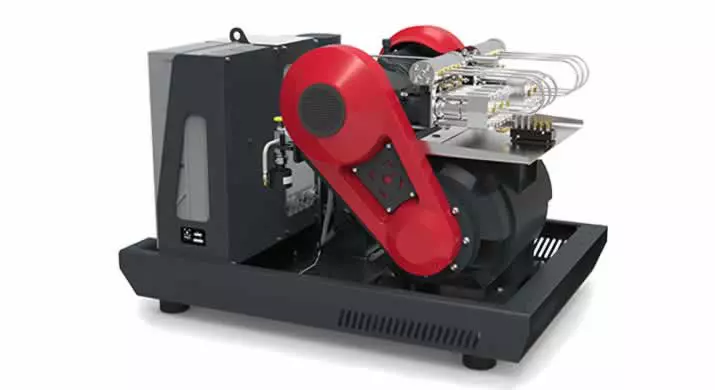
BOCAL DE JATO DE ÁGUA ABRASIVO
Todos os bocais de jato de água abrasivos utilizam o mesmo princípio de funcionamento básico que o bocal de jato de líquido, patenteado pela primeira vez em 1936 (Patente 2,040,715). A configuração moderna é mostrada no diagrama à direita.
Note-se que para um bocal só de água que é concebido para cortar materiais moles, a câmara de mistura e o tubo são eliminados, e o jato coerente de água corta o material sozinho.
Para que o bocal de jato de água abrasivo possa cortar eficientemente e aumentar a vida útil dos componentes, é fundamental que o orifício da joia seja cuidadosamente alinhado no corpo do bocal. Todos os bocais da OMAX são alinhados de fábrica e testados individualmente para assegurar um corte eficiente e uma longa vida útil.
RELATED QUESTIONS
Most of the maintenance on an abrasive waterjet involves servicing the pump and the cutting head. The exact type and frequency of maintenance will depend on how the machine is used (pump pressure, type of material cut, etc.) the specific components (pump type, nozzle type, accessories) and the water quality. The nozzle needs to be changed out fairly frequently to ensure precision cutting. Changing out a nozzle takes just a few minutes. Our MAXJET 5i nozzle is warranted to last 500 operating hours. The wear components in the cutting head need to be changed out occasionally. This takes approximately 10 minutes. The high pressure pump needs regular servicing. Our direct drive pumps are very easy to service and, depending on the pump model, a rebuild typically takes 1-2 hours. Accumulated abrasive and work material particles need to be regularly removed from the tank. The table slats should be inspected for wear at least once a month and rotated or replaced when worn.
What to do with that used abrasive tends to fall into three categories: disposing, recycling, and repurposing. In most cases, used abrasive from a waterjet can be thrown out with other non-toxic garbage since garnet is a non-reactive, natural substance. However, if the abrasive has been used to erode toxic material and is contaminated with particles of toxic material such as lead or beryllium, it can't be simply thrown out with the trash and must be treated as toxic waste. A service that will periodically collect and properly dispose of your used abrasive can be employed to simplify this process.
Cutting speed for abrasive waterjets is affected by multiple factors, including material type, material thickness, desired edge quality, part geometry, pump horsepower and more. Compared to other cutting processes, abrasive waterjets cut 5-10 times faster than wire EDM when cutting material less than 1 inch thick, and generally not as fast as plasma and laser cutters.
Table accuracy for OMAX line waterjets is ±0.0010", for MAXIEM line waterjets is ±0.0030", for GlobalMAX line waterjets is ±0.0030" and ProtoMAX is ±0.0050". The repeatability for the tables in both lines is ±0.0010". Be aware that more than just the X-Y accuracy of a table goes into the final accuracy of a part cut on an abrasive waterjet. This is due to the nature of the cutting tool on an abrasive waterjet, a high velocity stream of water and abrasive known as the jetstream. Unlike rigid cutting tools, the jetstream bends as it moves and the lower part of the jetstream doesn't behave exactly like the upper part. The width changes and deforms and it tapers as it cuts. All of these things change with different materials, different thicknesses, different cutting speeds and a range of other factors. The control software on all OMAX abrasive waterjets uses an advanced cutting model that takes all of these factors into account and for each cutting job and optimizes the cutting parameters to make accurate parts every time. To get a precise measurement of accuracy for any abrasive waterjet system, get some test cuts done with your part designs and material and measure them.