The OMAX 55100 is an excellent fit for shops needing a machine with a smaller footprint but capable of cutting medium-sized stock.
- Cutting envelope of 8' 4" x 4' 7" (2.54 m x 1.39 m)
- ±0.001" (±0.025 mm) linear position accuracy
- Backed by our exclusive IntelliMAX Premium Software
- Pre-loaded linear bearings and precision ball screws
- Standard programmable Motorized Z-Axis with a precision OMAX MAXJET 5i Nozzle boosts productivity and process efficiency
- Standard Rapid Water Level Control for cleaner, safer, and quieter submerged cutting completes most work below 80 dBA
- Standard 600 lb Bulk Abrasive Delivery System transports garnet from the assembly's large hopper into the Zero Downtime Hopper located on the Z-Axis
- Designed and manufactured at the OMAX factory in Kent, Washington, USA
- Does not create heat-affected zones or mechanical stresses
- Machines a wide range of materials and thicknesses, from metals and composites to glass and plastics
- No tool changes & minimal fixturing dramatically reduce setup
DIMENSIONS & SPECS
Footprint (with pump) | 15' 1" x 8' 9" (4.60 m x 2.44 m) |
---|---|
Height (with scissor plumbing) | 10' (3.05 m) |
Operating Weight | 21,147 lb (9,592 kg) |
Weight (tank empty) | 7,960 lb (3,611 kg) |
X-Y Cutting Travel* | 8'4" x 4'7" (2.54 m x 1.39 m) |
Z-Axis Travel (with Motorized Z Axis)* | 8" (203 mm) |
Table Size | 10'6" x 5'5" (3.20 m x 1.65 m) |
Material Supports Slats | 4" x 1/8" Galvanized Steel |
---|---|
Maximum Supported Material Load | 400 lbs/sq ft (1,950 kg/sq meter) |
Electrical Requirements | 3-Phase, 380-480 VAC ±10%, 50-60 Hz |
Noise Level | Below 80 dBA at one meter for submerged cutting |
Speed | 180 in/min (4,572 mm/min) |
Linear Positional Accuracy* | ±0.001" (±0.025 mm) |
Repeatability* | ±0.001" (±0.025 mm) |
Ballbar Circularity* | ±0.0025" (±0.064 mm) |
* Accessories may reduce travel. Accuracy specifications are at 72° F (22° C).
PUMP INFO
Maximized uptime with 1,000 hours between maintenance cycles
Increased production by delivering 30% more cutting power
Variable Frequency Drive reduces startup power consumption and maximizes operating flexibility
EnduroMAX 100 HP | EnduroMAX 50 HP | EnduroMAX 30 HP | DynaMAX 575P | |
---|---|---|---|---|
Motor Power | 100 HP (75 kW) | 50 HP (37kW) | 30 HP (22 kW) | 75 HP (56 kW) |
MAX Jet Power | 85 HP (63 kW) | 42.5 HP (31.5 kW) | 25.5 HP (18.7 kW) | 51.6 HP (37.9 kW) |
Output Pressure | 60,000 psi | 60,000 psi | 60,000 psi | 60,000 psi |
Orifice & Flow Rate ** | 0.022" / 2.25 gpm (0.56 mm / 8.52 lpm) |
0.016" / 1.20 gpm (0.41 mm / 4.54 lpm) |
0.012" / 0.67 gpm (0.30 mm / 2.54 lpm) |
0.017" / 1.5 gpm (0.43 mm / 5.68 lpm) |
Footprint LxWxH | 44" x 62" x 44" (1,118 mm x 1,575 mm x 1,118 mm) |
66" x 36" x 38.5" (1,676mm x 914mm x 978mm) |
66" x 36" x 38.5" (1,676mm x 914mm x 978mm |
40" x 79" x 59" (1016 mm x 1996 mm x 1509 mm) |
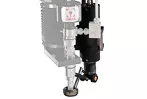
Collision Sensing Terrain Follower
The Collision Sensing Terrain Follower is an essential tool for working with uneven surfaces.
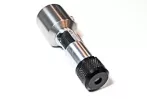
Laser Feature Finder
The Laser Feature Finder allows for visual reference before introducing water and garnet.
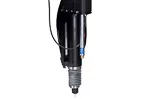
OMAX Drill Head
Achieve reliable piercing of composites and laminates with an OMAX-Engineered pneumatic drill.
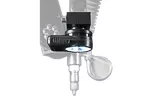
Precision Optical Locator
The Precision Optical Locator is designed to let you accurately place parts on the OMAX for secondary machining operations.
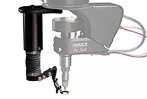
Terrain Follower
Used with the AJet cutting head, the Terrain Followers adjusts standoff to compensate for irregularities in the material surface.
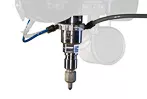
Vacuum Assist
The OMAX Vacuum Assist is ideal for piercing brittle materials, advanced composites, challenging laminates, and more.
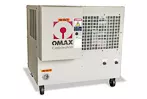
Chiller System
OMAX Chiller supplies inlet water at a consistent temperature extending pump seal life for longer, sustainable production.
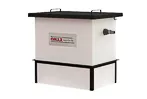
Laminar Filter
The Laminar Filter cleans overflow required for recycling through a closed loop system or for sanitary disposal.
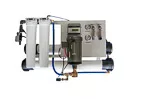
Reverse Osmosis System
The Reverse Osmosis System can remove 90% of total dissolved solid in water.

Water Recycling System
The OMAX Water Recycling System captures and reuses workable overflow water.
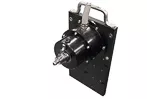
Rotary Axis
The Rotary Axis allows for 6-axis paths to create complex 3D shapes in tube, pipe, and bar stock.
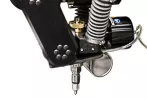
TiltaJET
The TiltaJET lets the OMAX JetMachining Center achieve virtually zero taper.
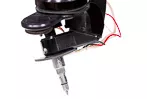
AJet
With a cutting range from 0° to 60°, the AJet can easily cut beveled edges, angled sides, and countersinks.