The MAXIEM 2040 abrasive waterjet system is designed for shops with high-capacity production demands.
- Cutting envelope of 13' 10" x 6' 7" (4.21 m x 2.00 m)
- ±0.003" (±0.076 mm) linear position accuracy
- Backed by our exclusive IntelliMAX Standard Software
- Powerful all-in-one controller computer with large 23" screen
- Standard IntelliTRAX traction drive inside the X-Y Axis beams fully enclosed inside coated steel covers
- Standard programmable Motorized Z-Axis with a precision OMAX MAXJET 5i Nozzle boosts productivity and process efficiency
- Standard scissor-style hard plumbing
- Designed and manufactured at the OMAX factory in Kent, Washington, USA
- Does not create heat-affected zones or mechanical stresses
- Machines a wide range of materials and thicknesses, from metals and composites to glass and plastics
- No tool changes & minimal fixturing dramatically reduce setup
DIMENSIONS & SPECS
Footprint (with pump & controller) | 21' 9" x 12' 11" (6.63 m x 3.94 m) |
---|---|
Height (with scissor plumbing) | 8' 10" (2.69 m) |
Operating Weight | 28,283 lb (12,829 kg) |
Weight (tank empty) | 8,500 lb (3,856 kg) |
X-Y Cutting Travel* | 13' 10" x 6' 7" (4.21 m x 2.00 m) |
Z-Axis Travel (with Motorized Z Axis)* | 12" (304 mm) |
Table Size | 16' 1" x 7' (4.90 m x 2.13 m) |
Material Supports Slats | 40 4" x 14Ga Galvanized Steel(102 mm x 2 mm) |
---|---|
Maximum Supported Material Load | 300 lbs/sq ft (1,465 kg/sq meter) |
Electrical Requirements | 3-Phase, 380-480 VAC ±10%, 50-60 Hz |
Noise Level | Below 80 dBA at one meter for submerged cutting |
Speed | 500 in/min (12.70 m/min) |
Linear Positional Accuracy* | ±0.003" (±0.076 mm) |
Repeatability* | ±0.001" (±0.025 mm) |
* Accessories may reduce travel. Accuracy specifications are at 72° F (22° C).
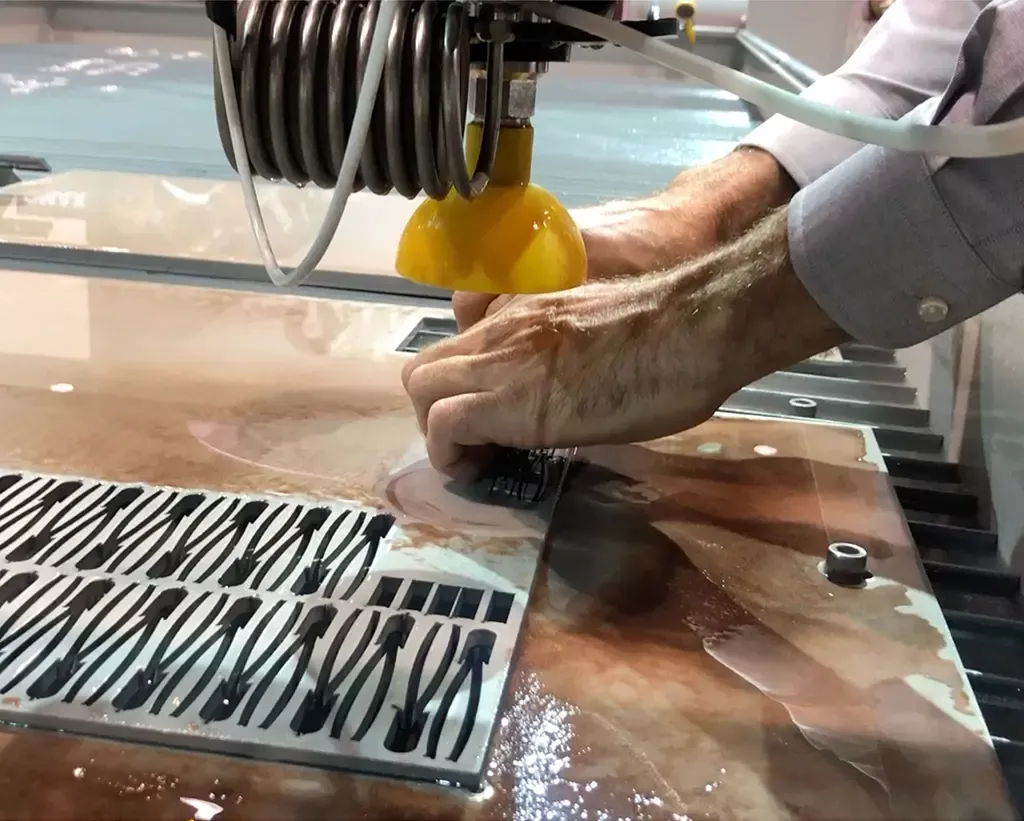
PUMP INFO
Continuous 50,000psi operation for faster part processing
Reliable design capable of over 500 cutting hours between maintenance cycles
Advanced pump technology lowers operating costs and increases pump operating life
MAXIEM 40 HP | MAXIEM 30 HP | MAXIEM 20 HP | DynaMAX 330 | |
---|---|---|---|---|
Motor Power | 40 HP (30 kW) | 30 HP (22 kW) | 20 HP (15 kW) | 30 HP (22 kW) |
MAX Jet Power | 34 HP (25 kW) | 25.5 HP (19 kW) | 17 HP (12.5 kW) | 20.6 HP (15.1 kW) |
Output Pressure | 50,000 psi | 50,000 psi | 50,000 psi | 60,000 psi |
Orifice & Flow Rate ** | 0.015" / 1.09 gpm (0.41 mm / 4.13 lpm) | 0.014" / 0.84 gpm (0.36 mm / 3.18 lpm) | 0.011" / 0.52 gpm (0.28 mm / 1.97 lpm) | 0.011" / 0.6 gpm (0.28mm / 2.3 lpm) |
Footprint LxWxH | 52.5" x 31" x 42" (1,334 mm x 787 mm x 1,067 mm) | 52.5" x 31" x 42" (1,334 mm x 787 mm x 1,067 mm) | 52.5" x 31" x 42" (1,334 mm x 787 mm x 1,067 mm) | 43" x 53" x 40" (1090 mm x 1350 mm x 1010 mm) |
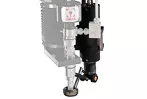
Collision Sensing Terrain Follower
The Collision Sensing Terrain Follower is an essential tool for working with uneven surfaces.
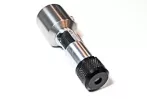
Laser Feature Finder
The Laser Feature Finder allows for visual reference before introducing water and garnet.
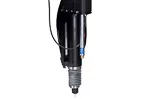
OMAX Drill Head
Achieve reliable piercing of composites and laminates with an OMAX-Engineered pneumatic drill.
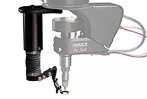
Terrain Follower
Used with the AJet cutting head, the Terrain Followers adjusts standoff to compensate for irregularities in the material surface.
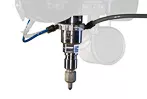
Vacuum Assist
The OMAX Vacuum Assist is ideal for piercing brittle materials, advanced composites, challenging laminates, and more.
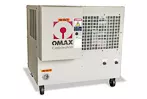
Chiller System
OMAX Chiller supplies inlet water at a consistent temperature extending pump seal life for longer, sustainable production.
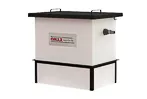
Laminar Filter
The Laminar Filter cleans overflow required for recycling through a closed loop system or for sanitary disposal.
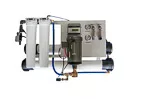
Reverse Osmosis System
The Reverse Osmosis System can remove 90% of total dissolved solid in water.

Water Recycling System
The OMAX Water Recycling System captures and reuses workable overflow water.
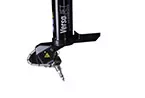
VersaJet
VersaJET has a cutting range of 0 to 60 degrees for cutting beveled edges, angled sides, countersinks and complex 3D shapes.