
LEARN ABOUT WATERJETS
LEARN ABOUT WATERJETS
HOW DOES WATERJET CUTTING COMPARE TO OTHER CUTTING METHODS?
Waterjet cutting compares favorably with other cutting methods, offering good accuracy, fast set-up time and fast cutting, while also cutting a wide range of materials with no Heat Affected Zone (HAZ) or change in material properties.
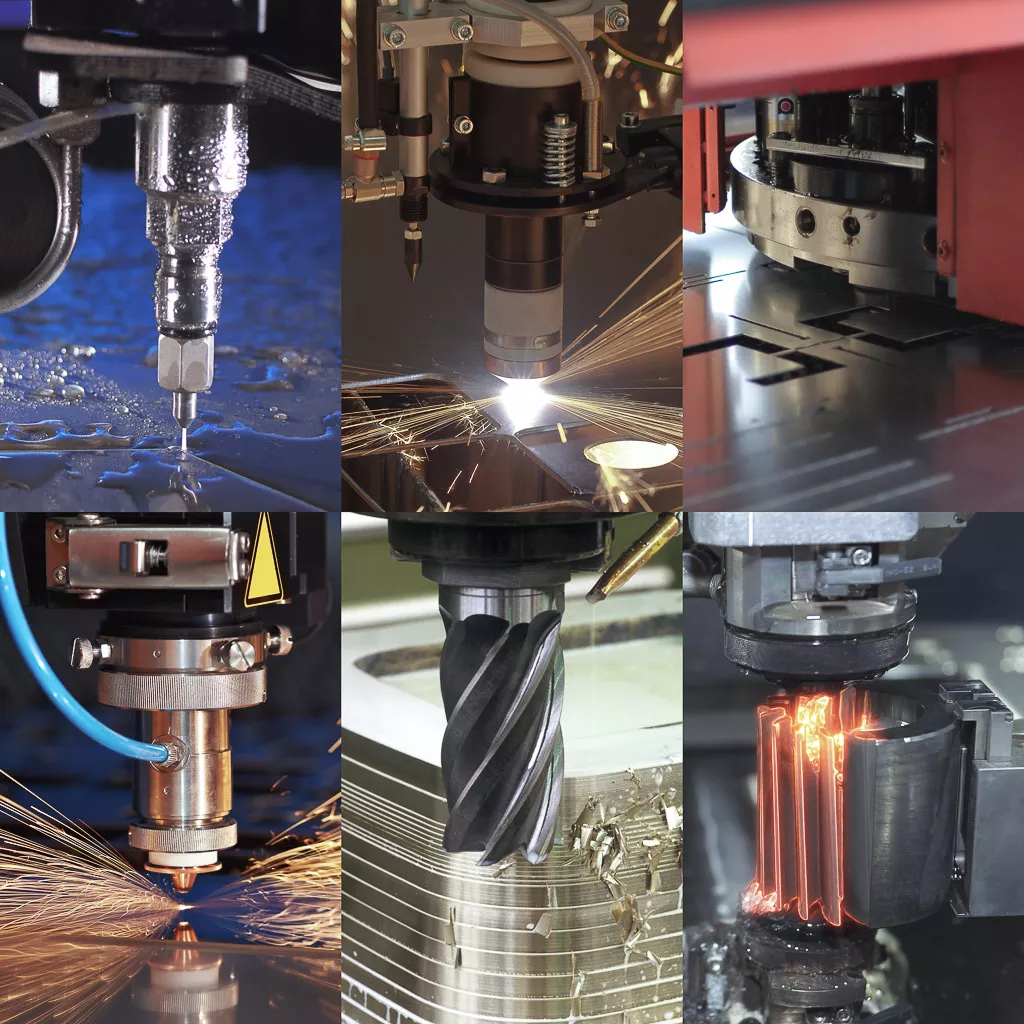
WATERJET |
WIRE EDM |
LASER |
PLASMA |
MILLING |
PUNCH PRESS |
|
---|---|---|---|---|---|---|
Accuracy |
Average of ±0.003" (±0.08 mm) and up to 0.001” (±25 μ) 1 | ±0.0001" (±2.5 μ) | ±0.001" (±25 μ) 2 2 | ±0.030 to ±0.060" (±0.75 to ±1.55 mm) | ±0.0003" (±8 μ) | Fair |
Thickness |
Up to 24" (61cm), virtually any material | 12" (30 cm) | Generally less than 0.25"(6.35mm) | Cuts less than 1.25" | Able to work on 3D parts |
Works well with thin sheets |
Cutting |
5-10 times faster than EDM when thickness is under 1" | 5-10 times slower than waterjet | Very fast cutting in thin, non-reflective materials | Fast with thin sheets | Fair | Fast batch production when initial programming and setup are done |
Edge |
Good | Excellent | Excellent | Fair | Excellent | Fair |
Material |
No Distortion 3 | No | Possible | Possible | No | Some |
Heat |
None | Some | Yes | Yes | None | None |
Material |
Works in virtually all materials except really hard ceramics | Only works in conductive materials | Only non-reflective metals 4 | Generally works in metals | Not ideal for very large parts | Not good for brittle or hardened materials |
Process |
Cold supersonic abrasive used to cut material | Spark erosion used to remove material from electrically conductive materials | Thermal process | Thermal process | Mechanical cutting tool | Shearing process |
Setup |
Fast and easy set-up | Relatively easy set-up | Relatively easy set-up but may have to tune laser for different materials | Relatively easy set-up | Time consuming set-up and programming | Time consuming set-up and programming |
FOOTNOTES
|
COMPLEMENT YOUR EXISTING MANUFACTURING PROCESS
Re-think Your Cutting Solution
Manufacturers from small job shops to large OEMs are finding that the OMAX abrasive waterjet cutting process is an ideal complement to their other manufacturing processes. In many cases the OMAX can quickly produce a complete final part, ready to go. However it can also produce a semi-finished or near-net-shape blank part suitable for secondary processing by conventional means. The abrasive waterjet process does not affect material properties, so the efficiency of conventional processes is not degraded. The close nesting capability of the OMAX maximizes material utilization. In addition, the OMAX is effective in many advanced and non-traditional materials where conventional processing may be a challenge.

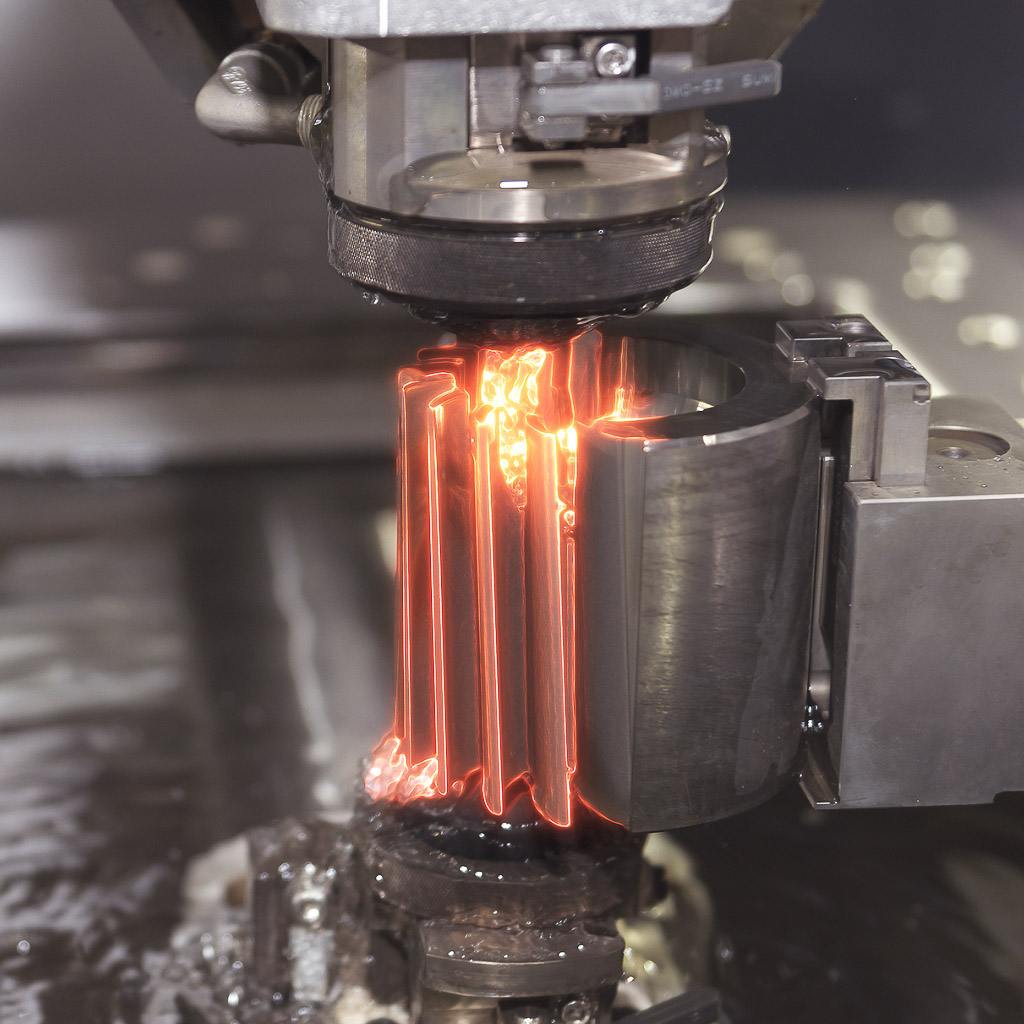
WIRE EDM
An OMAX system should not be viewed as a replacement for wire EDM, but rather as a complement. It is generally used by wire EDM shops to provide faster production where the ultra-high accuracy of wire EDM is not needed and to permit a shop to work with non-conductive materials such as composites and glass. It is also common to use an OMAX to produce a part to a general tolerance in the range of ±0.003" to 0.005” (±75µ to 125µ) and then use wire EDM to finish off areas where greater accuracy is required. The OMAX can also be used to quickly pierce starting holes for the wire EDM process.
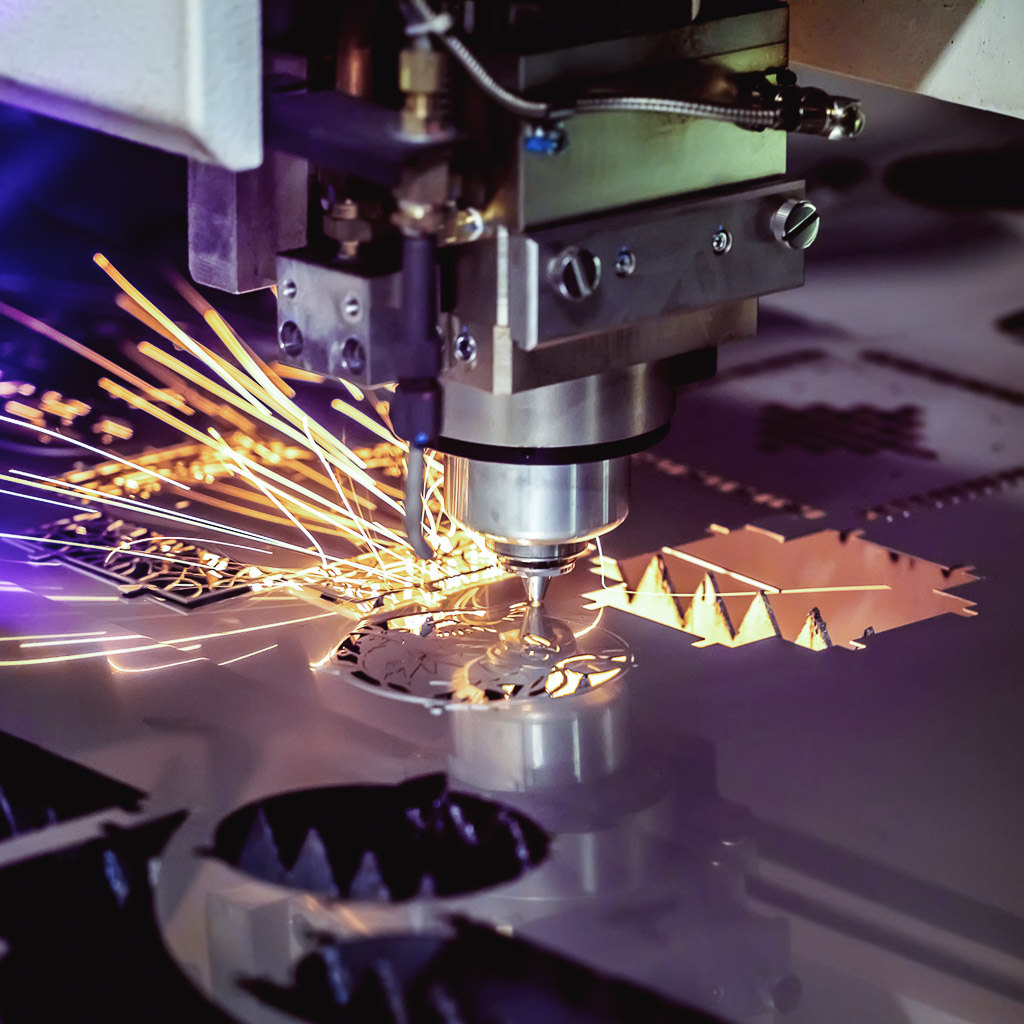
LASER
The key reason that laser shops and potential laser users buy an OMAX system is because it can work in a much wider variety of material and thicknesses. Advanced materials such as composites and laminates are easily cut on an OMAX, as are materials such as titanium or tool steel where the heat affected zone of a laser can be a problem. Thicker metals, such as aluminum, steel or stainless steel are also well-suited to the OMAX. It is common for laser specialty shops to purchase an OMAX simply to broaden their material capability. In addition an OMAX is typically one-third or less of the capital cost of a laser cutting system. This means that a shop that has been farming out work to a laser house can afford to buy an OMAX to bring the work in-house, thus saving money and improving scheduling and flexibility. It also means that a laser house can afford to purchase an OMAX to supplement their laser capability.
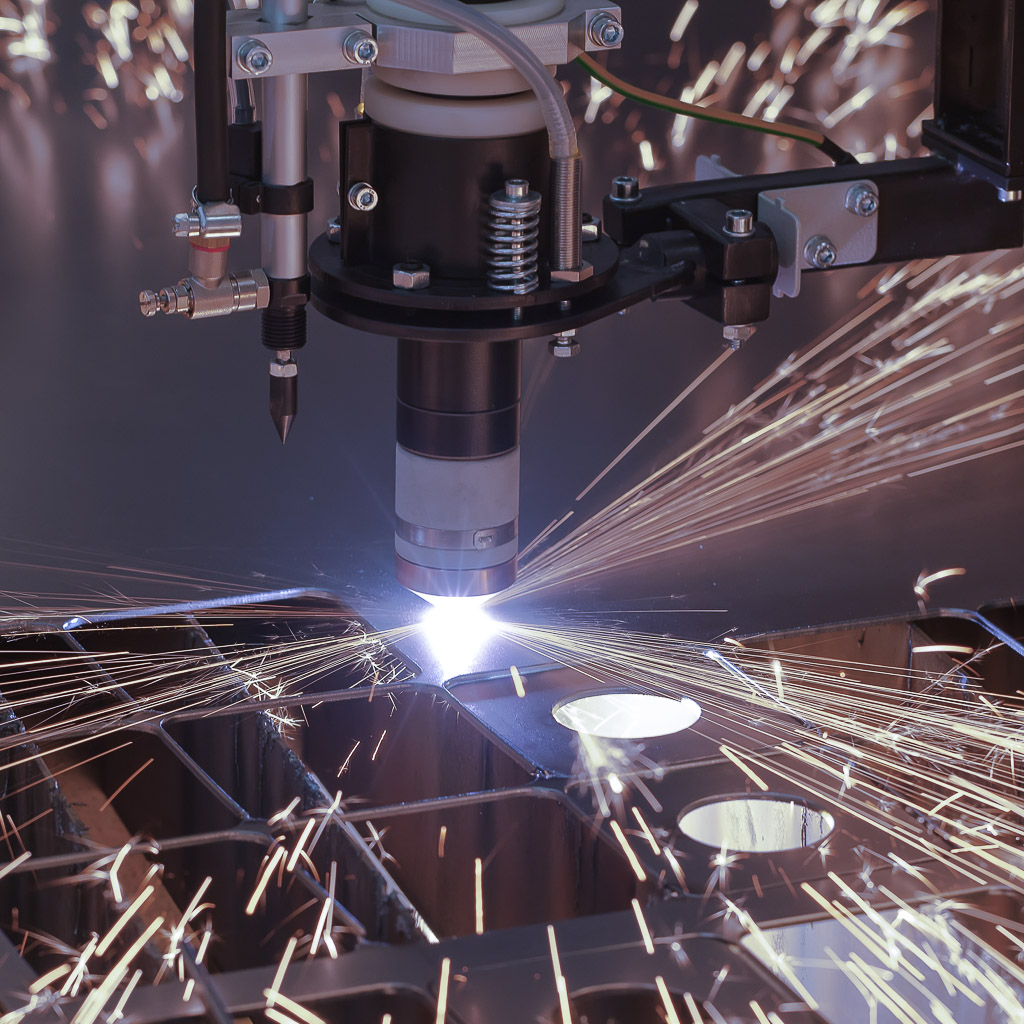
PLASMA
As in the case of lasers, the key reason that plasma users buy an OMAX is because it can work in a much wider variety of materials and thicknesses. Plasma cutting generally results in a relatively large heat affected zone and is limited in the materials it can cut. The OMAX, on the other hand, can cut virtually any material over a wide range of thickness without any heat affected zone. Advanced materials such as composites and laminates are easily cut on an OMAX, as are heat-sensitive materials such as titanium or tool steel. It is becoming common to use a plasma for rapid cutting of large blanks and then to use an OMAX Waterjet for precision cutting of holes and features, as the waterjet is more accurate.
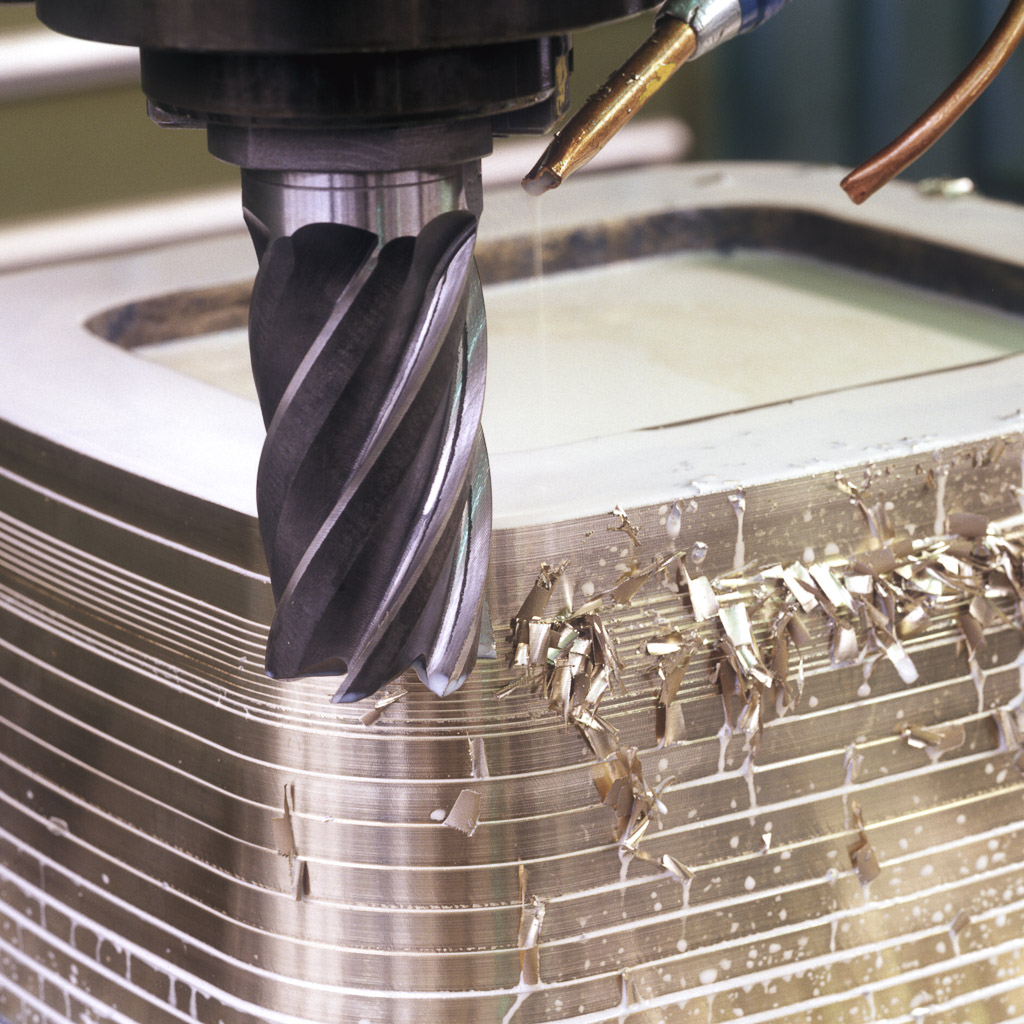
MILLING
Shops often use OMAX systems as a complement to their traditional mills and vertical machining centers. The OMAX is ideal for making short-run two-dimensional parts on a quick-turnaround basis and does not required a skilled machinist or specialized programmer. In addition the OMAX can save material by quickly making closely-nested near-net-shape blanks in preparation for final machining. The fact that the OMAX abrasive waterjet process does not change material properties means that secondary machining can be carried out efficiently with conventional cutting tools.

PUNCH PRESS
Shops generally purchase an OMAX to complement their traditional punch press when they need to work in a wider variety of material and thicknesses or need to make intricate shapes or closely-nested parts. Because of its very fast programming and set-up time, the OMAX is great for creating prototype parts and for short-run production.