The GlobalMAX 1508 is a compact, value-focused yet powerful abrasive waterjet.
- Cutting envelope of 2' 7' x 5' 0" (0.78 m x 1.52 m)
- ±0.003" (±0.076 mm) linear position accuracy
- IntelliMAX Global software uses our 4th generation cutting model to deliver the fast and efficient cutting
- Innovative Omega Drive System provides smoother transition from rotary motion to linear motion compared to traditional rack and pinion drive systems
- Omega Drive tooth engagement minimizes backlash and improves reliability
- Designed and manufactured at the OMAX factory in Kent, Washington, USA
- Does not create heat-affected zones or mechanical stresses
- Machines a wide range of materials and thicknesses, from metals and composites to glass and plastics
- No tool changes & minimal fixturing dramatically reduce setup
DIMENSIONS & SPECS
Footprint (with pump) | 5'3" x 11' 8" (1.60 m x 3.54 m) |
---|---|
Height (with whip plumbing) | 7'2" (2.18 m) |
Operating Weight (with water in tank) | 5400 lb (2449 kg) |
Weight (tank empty) | 3280 lb (1488 kg) |
X-Y Cutting Travel | 2'7" x 5' (0.78 m x 1.52 m) |
Z-Axis Travel | 5" (127 mm) |
Table Size | 2' 10" x 5' 5" (0.86 m x 1.64 m) |
Maximum Supported Material Load | 100 lbs/sq ft (488 kg/sq meter) |
---|---|
Electrical Requirements | Varies depending on configuration. (See pump specs.) |
Noise Level | Below 80 dBA at one meter for submerged cutting |
Speed | 500 in/min (12.7 m/min) |
Linear Positional Accuracy* | ±0.003" (±0.076 mm) |
Repeatability* | ±0.001" (±0.025 mm) |
Ballbar Circularity* | ±0.007" (±0.178 mm) |
* Accessories may reduce travel. Accuracy specifications are at 72° F (22° C).
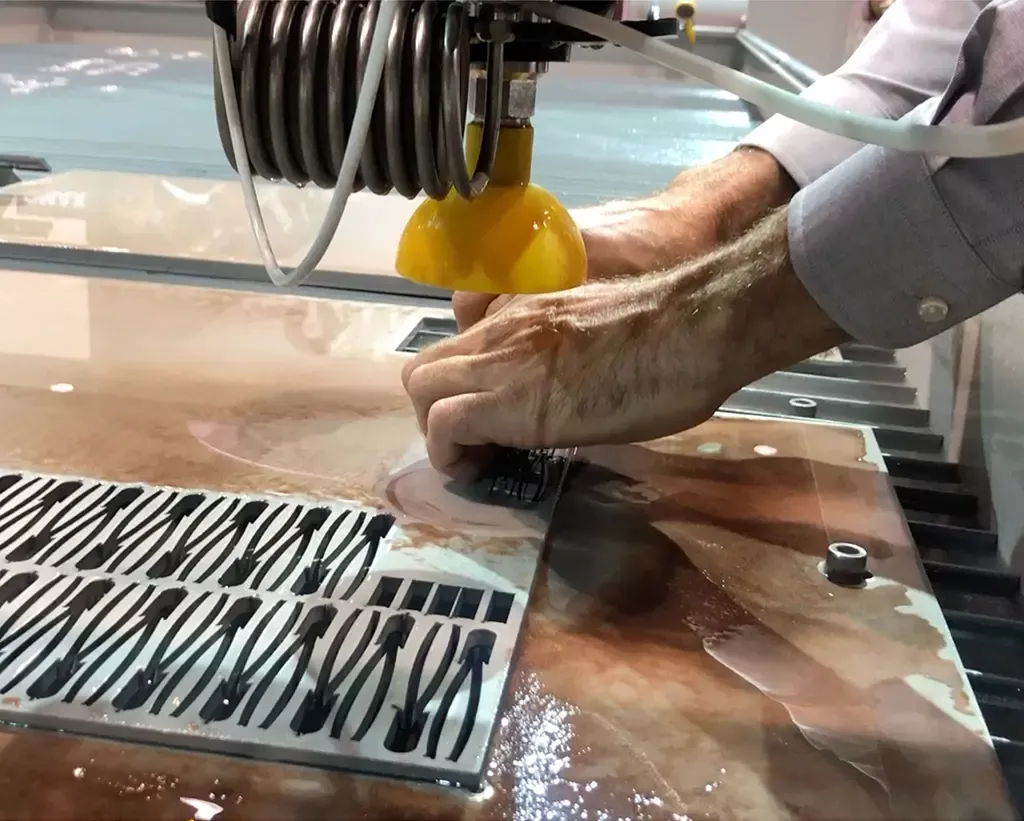
PUMP INFO
Direct Drive technology proven in thousands of installations worldwide
Efficient GlobalMAX pumps convert over 85% electrical power to pure cutting power
GlobalMAX 30 HP | GlobalMAX 20 HP | GlobalMAX 10 HP | |
---|---|---|---|
Motor Power | 30 HP (22 kW) | 20 HP (15 kW) | 10 HP (7.5 kW) |
MAX Jet Power | 25.5 HP (19 kW) | 17 HP (12.5 kW) | 7 HP (5.2 kW) |
Output Pressure | 45,000 psi | 45,000 psi | 30,000 psi |
Orifice & Flow Rate ** | 0.015" / 0.96 gpm (0.33 mm / 3.63 lpm) |
0.012" / 0.62 gpm (0.30 mm / 2.35 lpm) |
0.011" / 0.40 gpm (0.28 mm / 1.51 lpm) |
Footprint LxWxH | 52.5" x 31" x 42" (1,334 mm x 787 mm x 1067 mm) |
52.5" x 31" x 42" (1,334 mm x 787 mm x 1067 mm) |
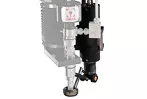
Collision Sensing Terrain Follower
The Collision Sensing Terrain Follower is an essential tool for working with uneven surfaces.
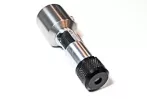
Laser Feature Finder
The Laser Feature Finder allows for visual reference before introducing water and garnet.
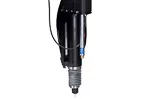
OMAX Drill Head
Achieve reliable piercing of composites and laminates with an OMAX-Engineered pneumatic drill.
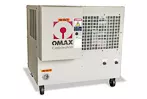
Chiller System
OMAX Chiller supplies inlet water at a consistent temperature extending pump seal life for longer, sustainable production.
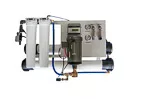
Reverse Osmosis System
The Reverse Osmosis System can remove 90% of total dissolved solid in water.

Water Recycling System
The OMAX Water Recycling System captures and reuses workable overflow water.