Customer Success: Cutting Services
Fabricación de componentes: impecable y económica
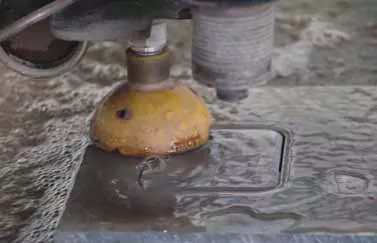
Werkzeug-Komponenten-Fertigung GmbH Sachsen (WKFS) utiliza principalmente máquinas herramienta CNC para fabricar componentes para herramientas, accesorios y la construcción de máquinas. Desde hace varios años, un potente sistema de chorro de agua JetMachining 60120 de OMAX que adquirieron a través de su distribuidor, INNOMAX AG, ha estado ampliando la gama de servicios de mecanizado de la empresa, ofreciendo una mejor rentabilidad y una mayor calidad en lo que respecta a la fiabilidad del proceso.
Los responsables de WKFS en Wilkau-Haßlau (Alemania) ven su empresa como el complemento ideal para los fabricantes de herramientas, moldes y máquinas: «En nuestra gama, tenemos principalmente máquinas grandes que los fabricantes de herramientas y máquinas normalmente no utilizan en sus talleres», explica Ulf Seifert, uno de los dos socios directores. «La división del trabajo entre las empresas de herramientas, moldes e ingeniería mecánica tiene sentido: fabricamos componentes grandes para clientes en toda Alemania y Europa en un plazo fijo, a unos precios justos y con una alta calidad, por lo que nuestros clientes pueden concentrarse en sus competencias básicas. »
Durante unos 20 años, los operarios de WKFS han estado produciendo piezas para una amplia variedad de industrias. «Producimos piezas únicas; rara vez sale la misma pieza dos veces», explica Seifert. «Por ejemplo, podemos fabricar piezas fresadas de hasta 3 x 7 m con un peso de la pieza de 50 toneladas, y podemos mecanizar piezas de trabajo de hasta 4 m de diámetro mediante el torneado vertical. Entre otras cosas, también fabricamos paneles de herramientas completos, como los que se utilizan para la construcción de herramientas de troquelado, por ejemplo».
Para Seifert y su socio Günther Tölle, es importante ser preciso al seleccionar los mejores procesos posibles para lograr los mejores resultados, tanto a nivel económico como tecnológico, en las correspondientes aplicaciones. «Es por este motivo que hace tres años ampliamos nuestra cadena tecnológica para incluir el corte por chorro de agua. Compramos un sistema JetMachining 60120 de OMAX a INNOMAX», explica Seifert. «Como proveedor de paneles de herramientas completos, este sistema nos ha permitido dar un salto significativo en la calidad».
Antes, las perforaciones de los paneles de herramientas se creaban mediante el corte por plasma. Sin embargo, esta tecnología suele ser demasiado imprecisa, sobre todo para las placas guía, por lo que teníamos que volver a fresarlas con el correspondiente aumento de los costes.
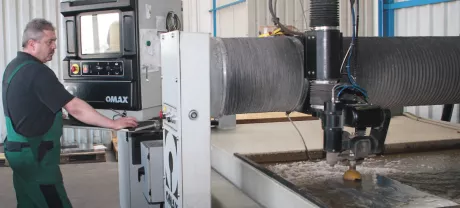
«Ahora podemos prescindir de este procesamiento posterior por completo. Con el sistema OMAX, podemos ofrecer unas perforaciones conforme a la alta calidad que nuestros clientes esperan de nosotros», explica Seifert. «Además, ya no tenemos que exponer los paneles al riesgo de la deformación térmica. Y eso es una gran ventaja en cuanto a la precisión. »
La JetMachining 60120 de OMAX procesa, entre otras cosas, chapas de aluminio y varios aceros para herramientas, incluidos los aceros pretemplados como el 1.2312. Pero los otros materiales tampoco suponen ningún problema para el corte por chorro de agua: desde los metales hasta las rocas y los materiales orgánicos, casi todos los materiales se pueden cortar con suma precisión con este proceso. «Las chapas intermedias suelen tener un espesor de entre 40 y 50 mm», afirma Seifert. «El desafío al que nos enfrentamos a diario es crear orificios muy complejos con los radios angulares más pequeños posibles».
En este caso, sin embargo, la física del chorro de agua tiene sus límites, pero con algunos trucos, el fabricante, OMAX, logra utilizar las leyes de la naturaleza en beneficio de sus usuarios. Por ejemplo, cuanto más gruesa es la chapa a cortar, más se estrecha el chorro de agua. Para poder seguir garantizando un corte exacto en ángulo recto, el cabezal giratorio Tilt-A-Jet® de OMAX permite unos ángulos de inclinación de hasta 9°, lo que basta para realizar un corte recto fiable con una precisión de hasta cinco centésimas de milímetro, en función del material y el espesor de la chapa.
Biseles precisos
Girar el cabezal también permite realizar cortes ligeramente cónicos. «Esto supone una gran ventaja, sobre todo en los orificios de la herramienta por los que caerán las piezas de chapa más adelante», añade Seifert. «Aquí se pueden ejecutar biseles muy precisos de 2° a 3°, lo que garantiza que las piezas caigan de forma segura». La tecnología del chorro de agua también es una ventaja cuando se cambian las herramientas, ya que también permite realizar orificios en los paneles más adelante sin ningún problema, como el endurecimiento (sobre todo en los aceros con un alto contenido de carbono) o la deformación que se produce durante el corte por plasma y requiere un repaso que se debe tener en cuenta.
La máquina de gran formato JetMachining 60120 de OMAX permite cortar chapas de metal de hasta 1,5 x 3 m y el sistema puede gestionar pesos de componentes de hasta 6 toneladas. «La bomba de transmisión directa puede manejar hasta 4150 bares, pero con nuestros cortes de funcionamiento continuo, unos 3800 bares son más que suficientes», explica Seifert. «Si no llega al límite, reducirá significativamente el desgaste».
En el metal, los cortes se hacen con granate abrasivo de bordes afilados que se añade al agua. Por lo tanto, las superficies cortadas parece que se hayan pulido con chorro de arena y, a menudo, no requieren ningún otro tratamiento.
«El sistema de chorro de agua de OMAX nos impresionó por su elevada disponibilidad», enfatiza Seifert. «Solo se deben sustituir las piezas que se desgastan. El servicio también es muy rápido y competente». Otra ventaja para Seifert es el sofisticado software: «Podemos importar modelos de volumen de casi todos los sistemas CAD/CAM», añade. «El software garantiza un modelo de corte optimizado, lo que nos permite conseguir unos resultados óptimos de forma rápida y fiable».