
LEARN ABOUT WATERJETS
WHAT IS A WATERJET?
A waterjet utilizes a high pressure stream of water to erode a narrow line in the stock material. Because the abrasive is added at the nozzle, it is simple to switch between water only and abrasive waterjet cutting. This flexibility greatly enhances the versatility of a waterjet machine, as it can easily switch from cutting ½" (1.27cm) foam gaskets to 4" (10.16cm) titanium brackets.
The waterjet cutting machine system consists of three basic components:

The Table
The table is an X-Y nozzle mechanism with garnet hopper attached and catcher tank below.

The Pump
The high pressure pump provides pressurized water for the cutting process.

The Controller
The controller uses software for system operation, motion control, and nozzle positioning.
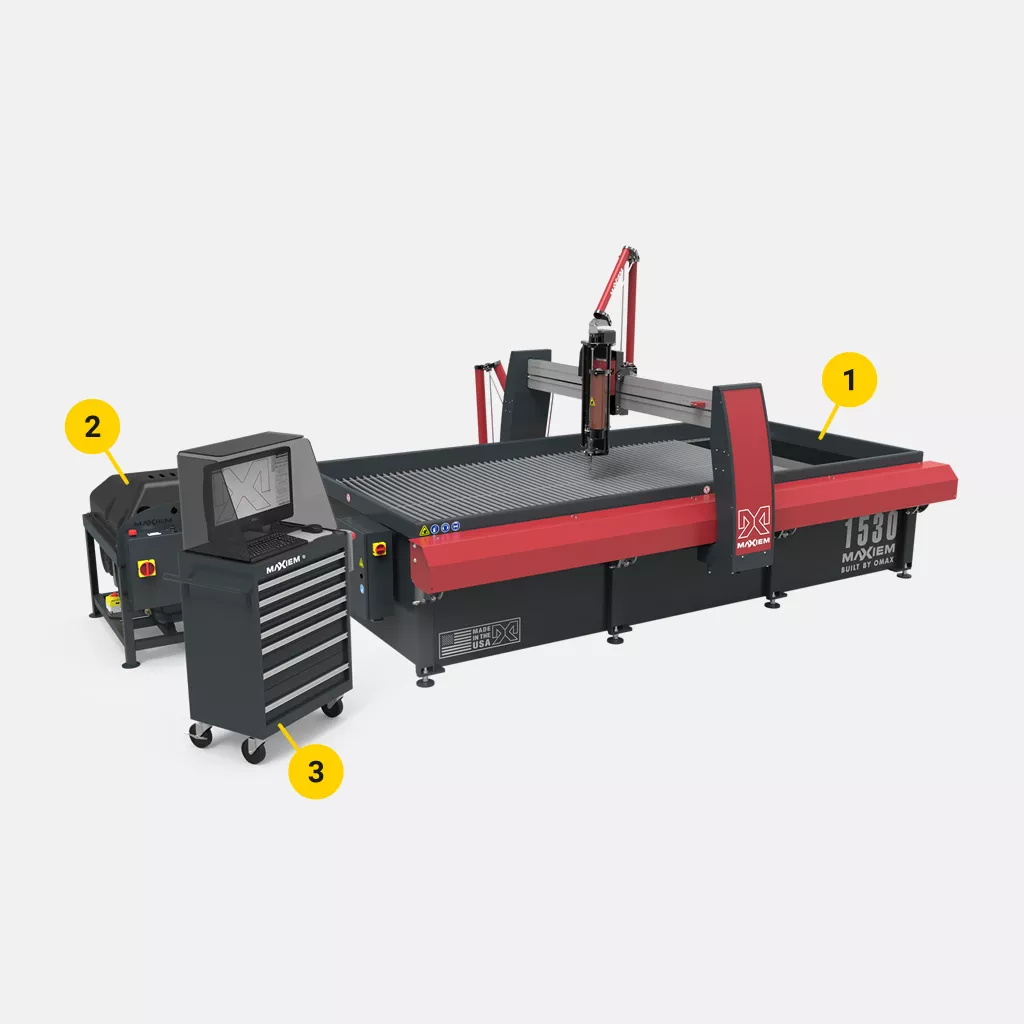
HISTORY OF WATERJETS
The Beginning
Using water as a cutting method for soft materials has been around for decades. Early forms such as the paper metering system by the Paper Patents Company in the 1930s used relatively low-pressure water. While early waterjets could easily cut soft materials, they were not effective in cutting harder materials. The ability to cut harder materials, such as metals, was achieved by adding an abrasive to the waterjet in the cutting nozzle after the jet stream was formed. But simply inducing garnet was not a viable solution without further advancements. Cutting harder material would take two innovations: ultra-high pressure pumps and advanced waterjet nozzles.
Technological Advances
High pressure waterjet technology took form in the post-World-War-II-era, resulting in faster cutting and greater precision. Reliability remained a challenge until the early 1970s when Dr. John Olsen, VP of Operations at OMAX Corporation, developed the first reliable ultra-high pressure pump.
Commercial Success
Early abrasive waterjet nozzle life was too short to be commercially viable, but material innovations in mixing tubes by Boride Corporation eventually resulted in a commercially acceptable nozzle. With the combination of a durable abrasive waterjet nozzle and a reliable high pressure pump, an abrasive waterjet machine could now cut a wide range of materials, including hardened tool steel, titanium, stone and glass.
Timeline
-
1930s
Low-pressure waterjet system used to cut paper. Abrasive waterjet nozzle concept patented.
-
1940s
High pressure seals developed for aviation & automotive hydraulics
-
1950s
Ultra-high pressure (100,000 psi, 6,900 bar) liquid jet used to cut aerospace metals
Numerical Control (NC) system developed by John Parsons
High pressure waterjet developed to cut plastic shapes
-
1960s
Up to 50,000 psi (3,450 bar) pulsing waterjet created at Union Carbide and cut metal and stone
High Pressure pumps manufactured for polyethylene industry
-
1970s
Bendix Corporation develops concept of using corundum crystal for waterjet orifice
Dr. John Olsen develops and patents the high pressure fluid intensifier
First mainstream commercial waterjet cutting system introduced
-
1980s
Boride Corp. develops ROCTEC ceramic tungsten carbide composite mixing tubes
Evolution of 1930s abrasives nozzle design brings abrasive jet machining to reality
-
1990s
OMAX Corporation established
Dr. John Olsen develops and patents (5,508,596 & 5,892,345) motion control systems to precisely locate the waterjet stream
-
2000s
Cutting model improvements significantly increase cutting speeds in OMAX machines
High precision zero taper waterjet cutting introduced with the Tilt-A-Jet
Affordable and versatile MAXIEM Waterjet line introduced
-
2010s
OMAX Rotary Axis and A-Jet brings 6-Axis machining to OMAX Machines
EnduroMAX Pump Technology significantly increases reliability
IntelliMAX Software Suite adds innovative system monitoring and advanced 3D tools
-
2020s
IntelliMAX upgraded for inter-connectivity, scripting, and advanced monitoring
OptiMAX Waterjet debuts introducing industry 4.0 software and technology to abrasive waterjet